Welding Aluminum with a Stick Welder: A Tough but Useful Skill
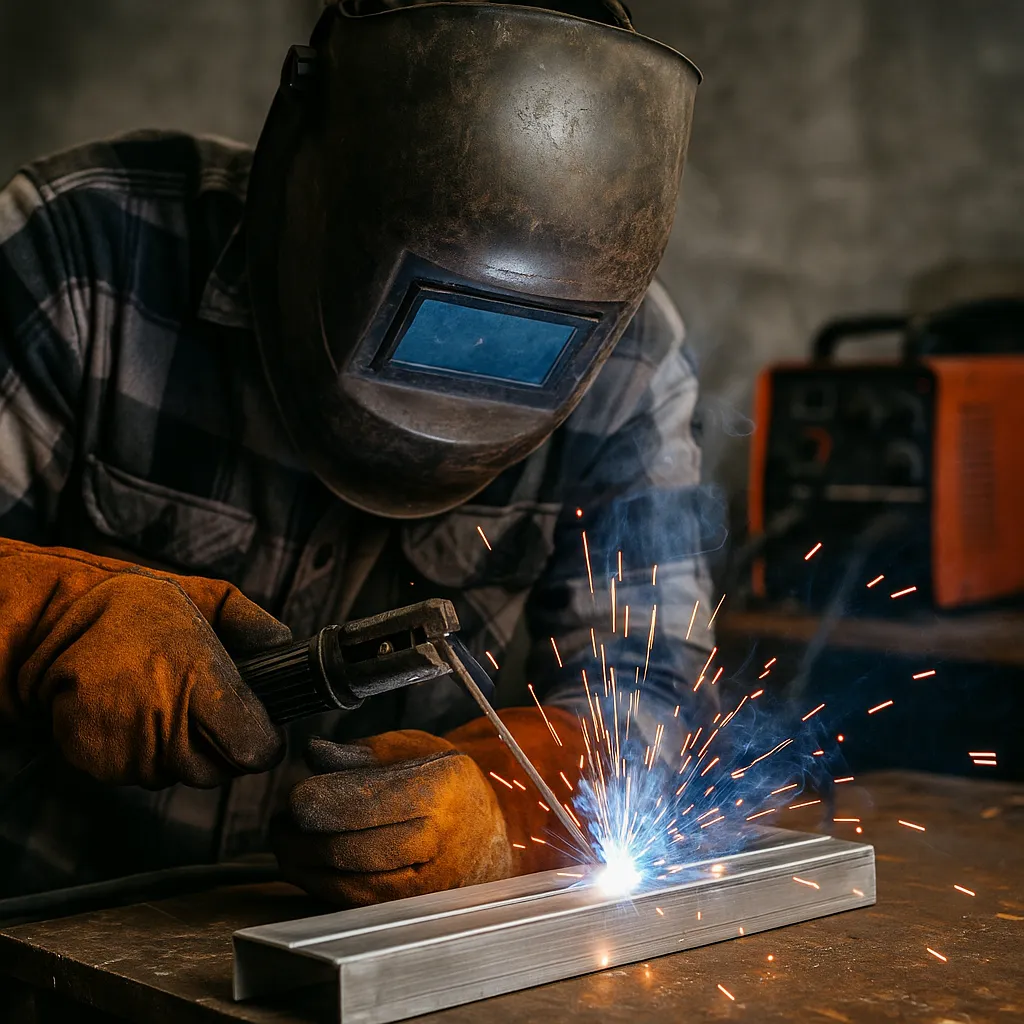
Disclosure: This post contains affiliate links. As an Amazon Associate, I earn from qualifying purchases—at no extra cost to you.
Stick welding isn’t the top choice for aluminum—but sometimes, it’s all you’ve got. Whether you’re fixing a cracked trailer, repairing a part on the go, or just experimenting in your garage, you can weld aluminum with a stick welder. It’s not the cleanest method, and there’s a learning curve, but for quick jobs or outdoor conditions, it works.
Here’s what to expect and how to get better results with the right prep, tools, and mindset.
Rod Choice and Arc Stability Make All the Difference
To weld aluminum successfully, E4043 rods are your best bet. They’re designed specifically for aluminum and run best on AC. Many welders have tried DC+ in a pinch, but AC usually gives smoother arc control and reduces the risk of overheating or burn-through.
Expect a hotter, brighter arc than what you’d get with steel. You’ll also deal with more spatter. Most welders crank their machines up to 150–200 amps, depending on rod size and the thickness of the metal.
A high-quality auto-darkening helmet helps a lot here. The arc is intense and reflective, so good visibility is a must.
Setup Matters—Clean Metal or Nothing
Aluminum is unforgiving when it’s dirty. You absolutely need to prep the surface by wire brushing off the oxide layer and wiping the metal clean with acetone. Skipping this step leads to porosity and weak welds.
Small 110V stick welders often struggle with aluminum. If you’re using one, don’t be surprised if it fails to penetrate properly. A 220V-capable machine or dual-voltage model gives you much better control and power.
Also, make sure you’re in a dry, clean space. Moisture or grease will ruin your weld faster than anything else.
It’s Not Easy, but It’s Doable with Practice
Welding aluminum with stick rods isn’t a beginner-friendly process. The puddle is harder to see, the rods can be finicky, and the results are messy. But if you’re doing quick field repairs or patching outdoor equipment, it can get the job done.
Community feedback shows that short passes and lower travel speed work better than trying to run long beads. It helps reduce warping and keeps the heat manageable. Many hobbyists report success with this method for things like mower decks, gates, or boat parts.
Be ready for a heavy cleanup. Aluminum stick rods leave behind thick flux that’s tough to chip off. It won’t be pretty, but if it holds, it counts.
When Stick Makes Sense (and When It Doesn’t)
If you already have a stick welder and only work with aluminum occasionally, this method is a decent solution. It’s especially useful for outdoor jobs, where shielding gas from MIG or TIG might blow away in the wind.
On the flip side, if you’re doing frequent aluminum work, stick welding isn’t the best long-term plan. A dedicated TIG machine or a MIG with a spool gun will give you cleaner welds, more control, and a much easier experience.
Stick welding aluminum is more of a workaround than a go-to solution—but sometimes, that’s exactly what’s needed.
Conclusion
Welding aluminum with a stick welder is possible—and in some cases, it’s the only option on hand. With the right rods, proper prep, and a strong enough machine, you can pull off solid welds for quick fixes or outdoor repairs. It’s not for the faint of heart, but with practice, it becomes a valuable skill to have.
If you weld aluminum regularly or need precision, a TIG or MIG setup is worth the upgrade. But if you’re just trying to patch something together in your garage or in the field, stick welding aluminum can absolutely work.