What Kind of Welder Do I Need to Weld Aluminum?
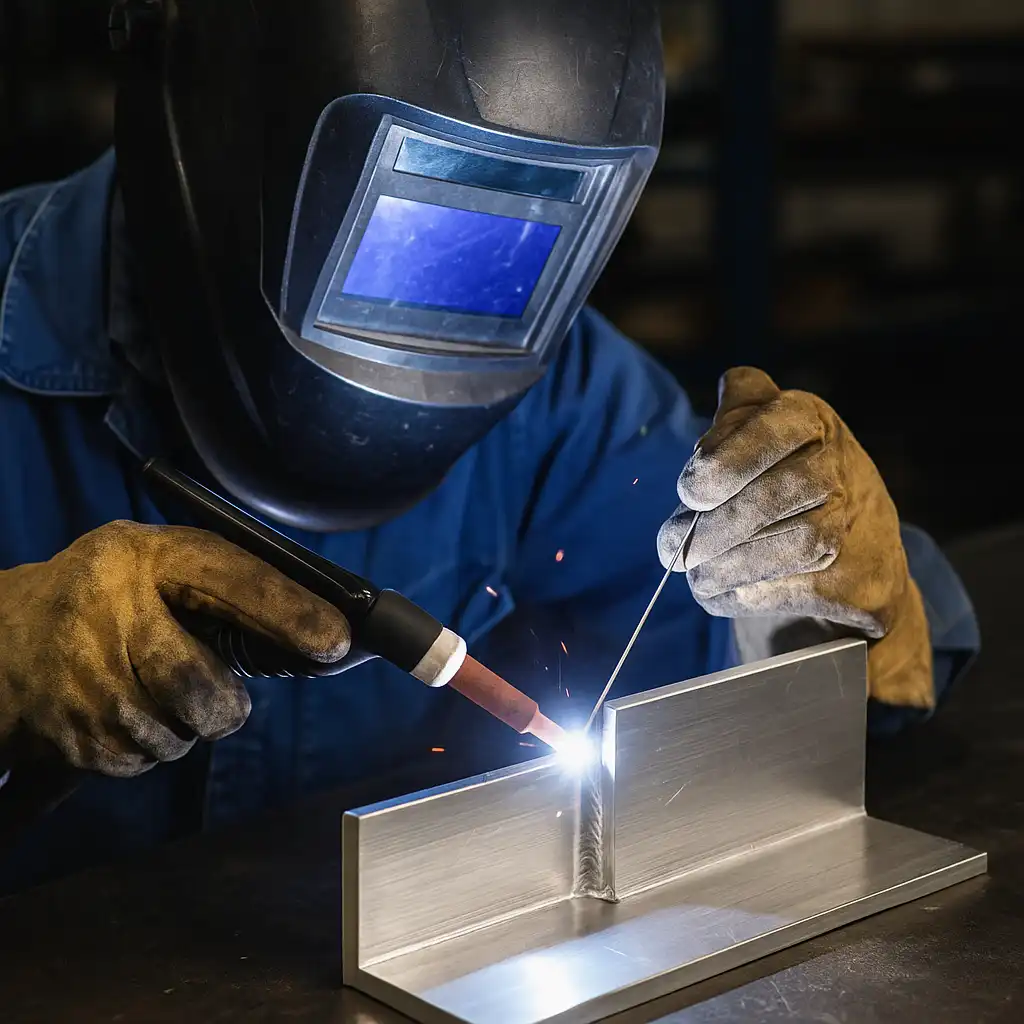
Welding aluminum requires a different approach compared to steel. Known for its lightweight nature and high thermal conductivity, aluminum poses unique challenges for welders. Whether you’re fabricating bike frames, repairing engine parts, or creating artistic pieces, choosing the right type of welder is essential to achieving clean, strong welds.
Understanding Aluminum’s Welding Characteristics
Aluminum has a lower melting point than steel and is more sensitive to heat input. It also oxidizes quickly when exposed to air, forming a coating that must be removed before welding. These properties influence the type of welder and technique needed. Improper equipment can lead to burn-through, poor bead quality, and weak joints.
TIG Welding for Precision and Clean Welds
Tungsten Inert Gas (TIG) welding is often considered the best choice for aluminum. It uses a non-consumable tungsten electrode and an external filler rod, with argon gas shielding the weld area. TIG welding is ideal for thin aluminum sheets and applications requiring high precision and aesthetic finish. However, it requires a higher skill level and a clean working environment.
Recommended Settings and Features for TIG Aluminum
For TIG welding aluminum, look for a machine with AC (alternating current) capability. AC helps break through the oxide layer and provides a stable arc. A square wave or advanced inverter TIG welder is even better, offering adjustable balance control and pulse features for enhanced results.
MIG Welding for Speed and Ease
MIG (Metal Inert Gas) welding is a faster method and easier for beginners. It’s more forgiving on thicker aluminum pieces and is widely used in fabrication shops and automotive repair. A spool gun is recommended for MIG welding aluminum to reduce wire feeding issues, especially with softer aluminum wires.
MIG Machine Requirements for Aluminum
Your MIG welder should support aluminum wire and allow fine-tuning of voltage and wire feed speed. Use 100% argon shielding gas and ideally a push-pull system or a spool gun to prevent bird-nesting. A multi-process welder with MIG capabilities can also be a good investment for versatile work.
When to Use Stick Welding or Alternatives
Stick welding is not recommended for aluminum because of its lack of precision and unsuitable electrode types. Instead, TIG or MIG should be your go-to options. For industrial or high-volume projects, automated welding systems or friction stir welding may be employed, but these are specialized techniques used mostly in manufacturing.
Conclusion
Choosing the right welder for aluminum depends on your project needs, skill level, and budget. TIG is ideal for precision and control, while MIG offers speed and accessibility for thicker materials. Selecting a machine with the proper features, especially AC output for TIG or a spool gun for MIG, is crucial to achieve quality aluminum welds.