Best Amperage for 7018 Welding Rod: Fine-Tune Your Settings for Cleaner Welds
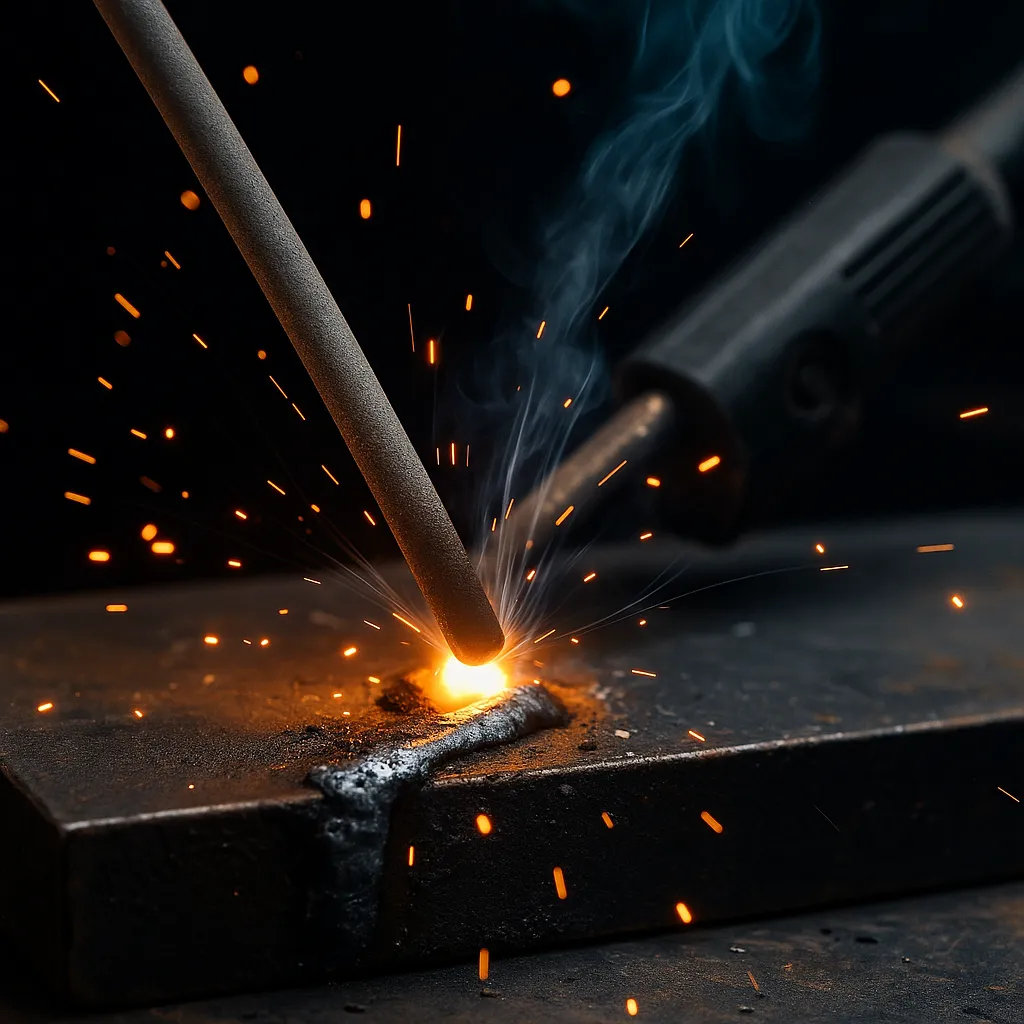
Getting your amperage dialed in can make or break your weld—especially when you’re working with 7018 rods. These low-hydrogen electrodes are a staple in structural work, fabrication, and general-purpose stick welding. But they only perform at their best when the amps are just right.
Let’s break down the best amp ranges for different rod sizes, how to tell when you’ve got the settings right, and a few real-world tips based on community feedback and manufacturer guidance.
Recommended Amperage by Rod Size
The amperage you use depends on the diameter of your electrode. Here’s a quick rundown:
- 3/32″ – 70 to 110 amps
- 1/8″ – 110 to 160 amps
- 5/32″ – 150 to 210 amps
- 3/16″ – 200 to 275 amps
If you’re using 1/8″ rods—which are super common for shop and structural work—most welders find that 125–135 amps hit the sweet spot. That range gives you a stable arc, solid penetration, and a bead that doesn’t require fighting the slag.
For vertical or overhead welds, dial it back about 10–15 amps. Lower heat gives you more puddle control and helps avoid sagging or dripping.
Getting a Smooth Arc
7018 rods are known for their buttery arc when everything’s tuned properly. But running too cold? That’ll make the rod stick and the bead look messy. Too hot? You’ll get excessive spatter and possibly warp thinner metal.
According to feedback from welding forums and user videos, most welders start low and increase amps slowly until the puddle flows well and the slag lifts easily. If your arc feels sluggish, add a few amps. If the bead’s flattening out or undercutting, pull back.
Equipment Compatibility and Setup Tips
Most stick welders—especially those with DC+ (electrode positive) output—can handle 7018 rods without issue. Some rods are also AC-compatible, which is useful for older transformer machines.
If your machine has Arc Force or Hot Start, those settings can make striking and maintaining the arc easier. This is especially helpful if you’re working at lower amperage on thinner material. For garage welders running on 120V, a 3/32″ rod at 90–100 amps is a practical option that still delivers solid penetration.
Just make sure your ground clamp is clean and firmly attached. Poor ground connection can rob your welder of valuable amps and cause erratic performance.
Safety Considerations and Practical Use
Cranking up the amps will give you deeper penetration, but it also increases your heat input. That means more risk of distortion—especially on thin stock.
Stick to the lower end of the amp range when welding lighter material. You can always make multiple passes rather than blowing through with one hot run. And for anything thicker than 3/8″, many welders preheat the metal to reduce cracking, especially on critical welds.
Don’t forget helmet shade and gloves. Shade 10–12 is typically ideal for 7018 work in this amp range, and you’ll want gloves that can handle extended arc time when you’re running hotter settings.
Conclusion
The best amperage for 7018 rods depends on the rod size, weld position, and the job at hand. For general flat-position welding, 1/8″ rods around 125 amps deliver solid results. If you’re working out of position or using thinner rods, back it down a bit for better control.
Pay attention to arc behavior, bead shape, and how the puddle moves. That feedback will guide your adjustments better than any chart. With the right settings, 7018 rods produce strong, clean, and reliable welds across a wide range of applications.