MIG vs TIG Welders: Key Differences Explained for Every Skill Level
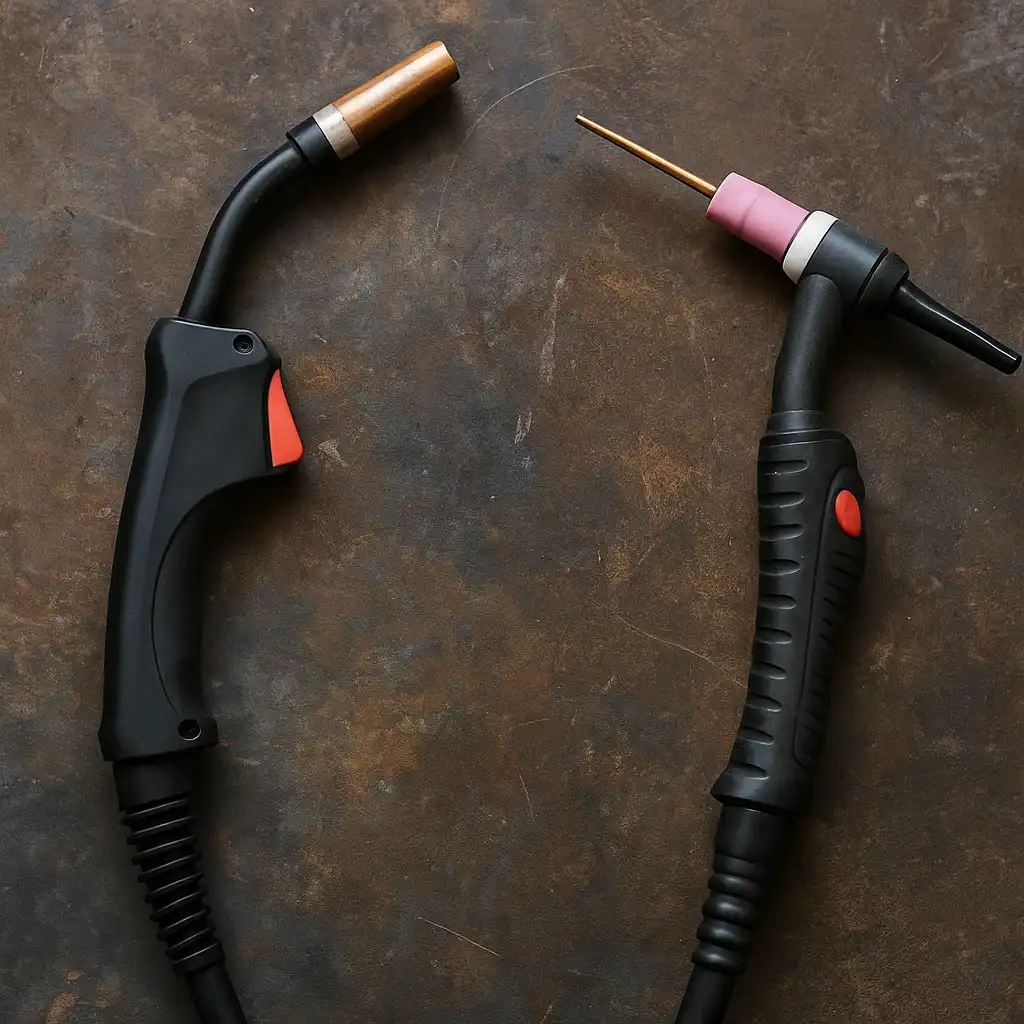
Metal Inert Gas (MIG) and Tungsten Inert Gas (TIG) welding are two of the most commonly used welding techniques in the industry, each offering unique strengths and applications. Whether you’re a beginner choosing your first welder or a seasoned professional deciding on a machine for a specific project, understanding the difference between MIG and TIG welders is essential for making the right choice.
What Is MIG Welding?
MIG welding uses a continuously fed wire electrode and a shielding gas to protect the weld from contamination. The process is semi-automatic, which means the welder controls the gun, but the machine feeds the wire and gas automatically. MIG welding is generally easier to learn and faster than TIG welding, making it a favorite for beginners and high-volume production tasks.
What Is TIG Welding?
TIG welding, on the other hand, uses a non-consumable tungsten electrode and requires the welder to feed filler material into the weld manually. It offers greater control and precision, making it ideal for detailed work, thinner materials, and non-ferrous metals like aluminum and magnesium. TIG welding also produces cleaner welds with less spatter, but it takes more time to master.
Equipment and Setup
MIG welders typically have a simpler setup, consisting of a spool gun, wire feed system, and shielding gas (often argon or a mix). They’re widely used for steel and can be adapted for aluminum with the right setup.
TIG welders require more components: a foot pedal, tungsten electrode, shielding gas (pure argon), and a filler rod. TIG torches are also more sensitive, requiring fine motor control and consistent hand-eye coordination.
Welding Speed and Efficiency
MIG welding is faster, which makes it suitable for thicker materials and longer welds. It’s the go-to process for fabrication shops and automotive repairs where speed is essential.
TIG welding is slower but offers unmatched precision. It’s often used in aerospace, art sculpture, bicycle frames, and other industries that demand flawless weld appearance and integrity.
Strength and Appearance
Both processes can produce strong welds, but TIG welds typically have a neater appearance due to the precise control. If visual appeal is critical — like in visible joints or artistic applications — TIG is often the preferred method.
MIG welding, while stronger in thicker metals, may leave more cleanup due to spatter and doesn’t provide as refined a finish without post-weld work.
Conclusion
Choosing between MIG and TIG welding depends on your project requirements, material type, and skill level. MIG is user-friendly and great for quick, strong welds on thicker materials. TIG demands more skill but rewards the welder with precision, cleaner finishes, and versatility on a wider range of materials. Understanding their differences can help you invest wisely in the right machine for your workshop.