How Does a Spot Welder Work: Precision Welding with Electric Force
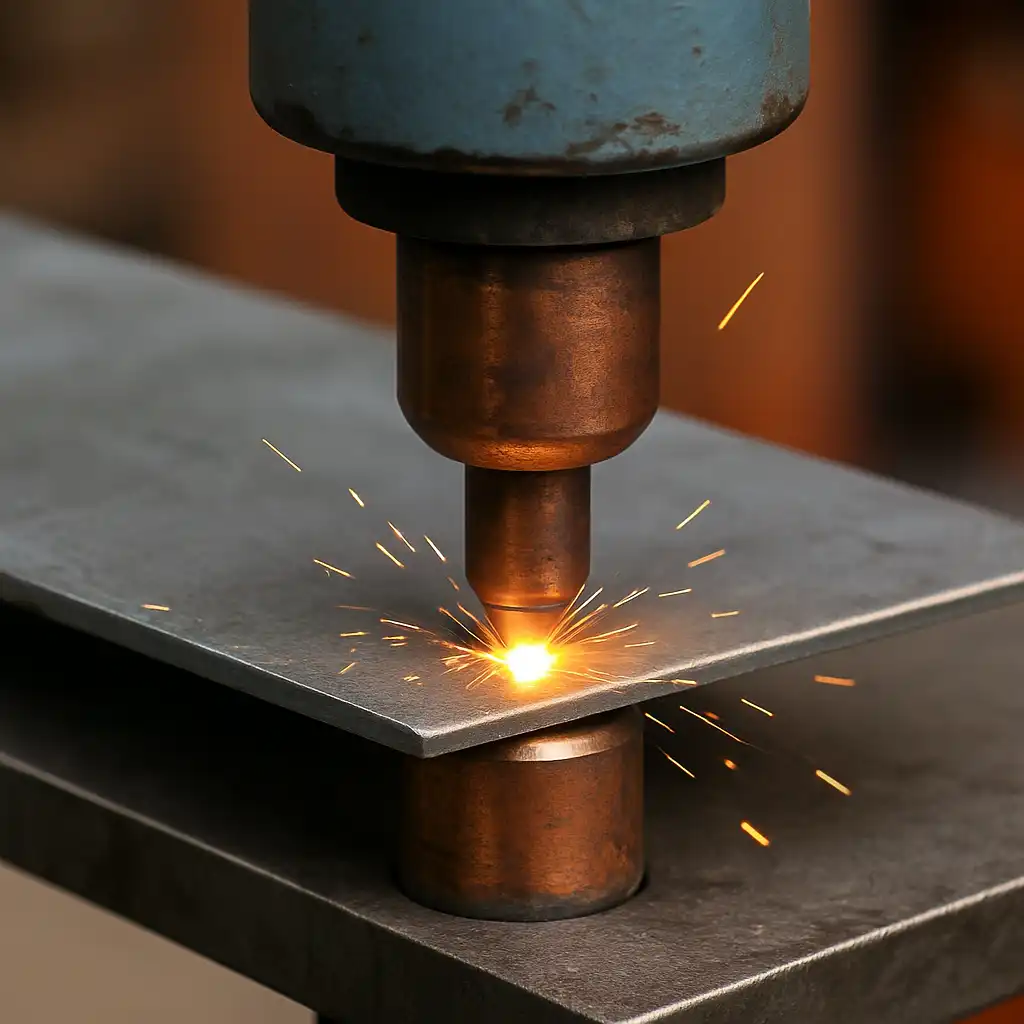
Spot welding is one of the most widely used joining methods in manufacturing and metalwork, especially when working with thin sheet metal. It’s the backbone of automotive assembly lines, metal enclosures, and even appliances. While it may seem like magic to fuse metal in just a few seconds without filler material, spot welding relies on a powerful combination of pressure and electric current to get the job done. Understanding how a spot welder works can help you make smarter equipment choices and better welds.
What Is Spot Welding?
Spot welding is a resistance welding process that uses two copper alloy electrodes to clamp two or more metal sheets together and pass a large electric current through the contact point. The current generates intense heat due to the metal’s resistance, causing the material to melt and form a weld nugget. Once the current stops, the metal cools and solidifies under pressure, resulting in a strong joint.
This technique is best suited for steel and stainless steel sheets and is particularly effective when welding overlapping pieces. Spot welders come in handheld and benchtop versions, making them versatile tools in fabrication shops and production lines alike.
The Role of Electrodes
The heart of a spot welder lies in its electrodes. Made from copper alloys for their excellent conductivity and heat resistance, the electrodes deliver both the clamping force and the electrical current needed for welding. They also shape the weld by focusing the current and pressure at a specific point.
The electrodes must maintain perfect alignment and cleanliness. Any dirt, misalignment, or wear can lead to inconsistent welds, weak joints, or even burn-throughs. Regular maintenance is critical to ensure repeatable, high-quality spot welds.
How Heat and Pressure Work Together
Two key variables in spot welding are current and pressure. The welding machine pushes a high-amperage, low-voltage current (often in the range of thousands of amps) through the metal sheets. This high current generates resistance heat at the contact point, enough to melt the metal.
The electrodes simultaneously apply pressure to hold the sheets together. As the metal melts, the pressure helps control the weld size and integrity. After the current is stopped, the pressure continues for a brief hold time to allow the weld nugget to solidify. The result is a small, round spot weld, typically about 5 to 10 mm in diameter.
Advantages and Limitations of Spot Welding
Spot welding offers a range of advantages. It’s fast, efficient, and doesn’t require filler materials. It also minimizes distortion in thin sheet metal, which is why it’s ideal for automotive and HVAC applications. Moreover, automation-ready spot welders make mass production seamless.
However, it does have limitations. Spot welding is mostly restricted to thin sheet metal and requires access to both sides of the workpiece. It’s not suitable for thick materials or precise seam work and can struggle with dissimilar metals or heavily coated surfaces unless properly configured.
Conclusion
Spot welding is a clean and efficient solution for joining thin metal sheets quickly and consistently. By using electrical resistance and clamping pressure, a spot welder creates strong bonds with minimal material distortion. Whether you’re repairing panels or assembling components, knowing how a spot welder works can improve your technique, equipment selection, and final results.