What Is MIG Welding? A Hands-On Guide for Real-World Use
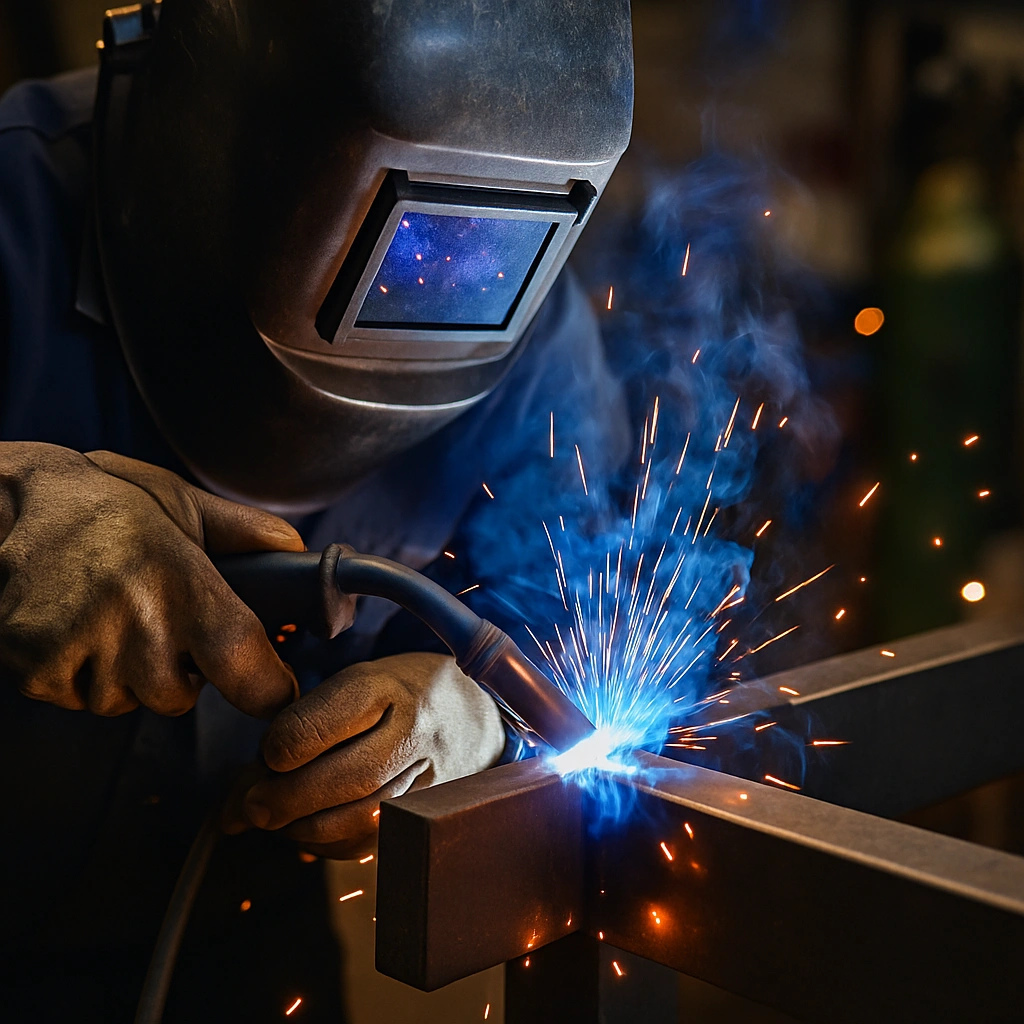
Disclosure: This post contains affiliate links. As an Amazon Associate, I earn from qualifying purchases—at no extra cost to you.
MIG welding is one of the most accessible and widely used welding methods—especially for home shops, small garages, and light fabrication. It’s quick to learn, works well on a variety of materials (especially mild steel), and doesn’t require advanced skills to produce strong, clean welds.
If you’re trying to decide whether MIG is right for your next repair or DIY project, here’s what you need to know.
What MIG Welding Actually Is and How It Works
MIG stands for Metal Inert Gas welding. It’s also called GMAW (Gas Metal Arc Welding). The process uses a spool-fed wire electrode that melts into the weld joint while a shielding gas protects it from air contamination.
You pull the trigger on the torch, and the machine does the rest—feeding the wire and managing the arc. It’s a continuous, semi-automatic process that makes it easier to focus on your technique rather than arc starts or rod feeding.
Most setups use a 75/25 argon and CO₂ gas blend, which provides good arc stability and keeps your welds clean.
Real Uses: What Welders Actually Do with MIG
MIG welding is everywhere—especially in garages, auto shops, and backyard projects. It works best on clean or lightly rusted mild steel, making it ideal for general-purpose fabrication and repairs.
Many welders use MIG for:
- Fixing mower decks, grills, or gates
- Replacing automotive body panels
- Building frames, carts, or tables
- Joining tubing or angle iron for shop projects
According to community feedback on welding forums and YouTube demonstrations, MIG is often the first welder someone buys—and the one they keep coming back to for everyday use.
Equipment Setup Tips and Compatibility
MIG welders come in both 120V and 220V versions. If you’re mainly working on thin to medium-gauge steel, a 120V unit with shielding gas is often enough. For thicker materials or more demanding projects, a 220V or dual-voltage model will give you more power and flexibility.
Some setups use solid wire with gas, while others rely on flux-core wire that doesn’t need gas. The trade-off? Flux-core is better for outdoor use but produces more spatter and slag.
A basic MIG setup includes:
- A grounded work clamp on bare metal
- .030″ or .035″ solid wire
- A cylinder of 75/25 gas (argon/CO₂)
- An auto-darkening welding helmet
- Gloves and flame-resistant gear for protection
Easy to Learn, Especially for New Welders
One of the biggest reasons MIG welding is so popular is the short learning curve. You can get a decent bead with just a few hours of practice. There’s no need to coordinate both hands or worry about filler rods.
Once your voltage and wire speed are dialed in, it becomes a rhythm-based process—focus on torch angle, travel speed, and consistency. Many beginners say MIG gave them the confidence to tackle small repairs within a day or two.
Even with its ease of use, safety still matters. Always work in a well-ventilated space, wear full PPE, and keep your work area clean to avoid fire hazards.
Conclusion
MIG welding is a solid choice for welders at any experience level. It’s fast, clean, and forgiving—perfect for auto repairs, home projects, and light fabrication.
- Pros: easy to set up, quick to learn, clean welds on steel
- Cons: not ideal for thick structural work or aluminum without extra gear
- Best for: garage DIYers, beginners, and anyone who needs reliable performance on mild steel
If you’re looking for a versatile method that doesn’t overcomplicate the process, MIG is a great place to start.