Can You TIG Weld Aluminum with DC Current? Tips That Actually Work
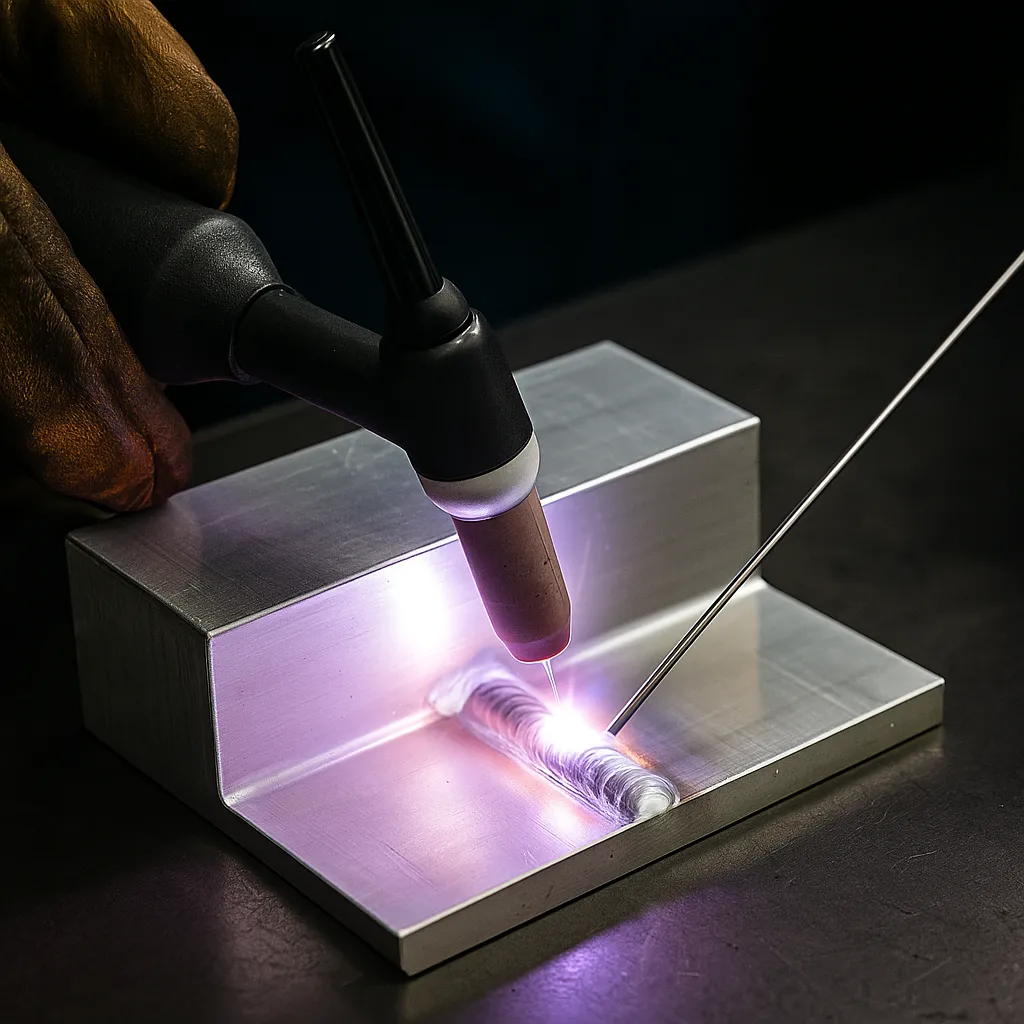
Disclosure: This post contains affiliate links. As an Amazon Associate, I earn from qualifying purchases—at no extra cost to you.
If you’ve only got a DC TIG machine and need to weld aluminum, you’re not out of luck—but you’re in for a bit of a challenge. While aluminum is typically welded using AC current, it is possible to do it with DC. You just have to know what you’re working with, prep properly, and adjust your expectations.
Let’s get into what makes it work, where it struggles, and how to get the best results using DC.
What Happens When You Weld Aluminum with DC?
Aluminum naturally forms an oxide layer that melts at a much higher temperature than the aluminum underneath. When you TIG weld with AC, the current alternates and helps break up that layer while also fusing the base metal.
DC welding doesn’t do that. With DCEN (Direct Current Electrode Negative), the current provides deeper penetration but no cleaning action. That means you’ll need to handle oxide removal manually before you even strike an arc.
Based on welding community feedback, DC TIG works best on thicker aluminum, where surface cleaning is possible and visual appearance isn’t a top concern.
Proper Prep Makes All the Difference
If you’re going to TIG weld aluminum with DC, surface prep is critical. That oxide layer has to go—completely.
Here’s what welders recommend:
- Scrub the joint with a dedicated stainless steel wire brush
- Wipe it down thoroughly with acetone or alcohol
- Avoid touching the cleaned surface with bare hands
On top of that, preheating the metal helps a lot—especially with thicker pieces. Most welders suggest heating to around 250–300°F. It softens the material, improves puddle control, and reduces the chance of cracking.
Use a 2% lanthanated tungsten electrode, and make sure you’re getting solid gas coverage. Argon flow around 15–20 CFH is standard for this setup. A gas lens with a large cup helps maintain coverage over a wider area.
DC Arc Behavior Feels Different
Compared to AC, the arc in DC mode is more focused and intense. It’s not forgiving, especially on thinner aluminum.
Welders often say that shorter arc lengths and slower travel help avoid overheating and puddle blowout. Expect a bit of a learning curve here—DC TIG on aluminum doesn’t behave like what you might be used to.
Also, don’t expect pretty welds. This technique is usually reserved for backside welds, non-visible joints, or quick field repairs where strength matters more than cosmetics.
When This Method Makes Sense
Not everyone has a machine with AC capability. If you’re working with a basic DC TIG unit—like the YesWelder TIG-205DS—DC welding might be your only option. And for one-off repairs or working on thick aluminum castings, it can be a useful trick.
That said, most welders agree: if you’re going to be welding aluminum often, get an AC/DC TIG welder. You’ll save time, get cleaner results, and avoid the stress that comes with DC-only work. Machines like the Everlast PowerTIG 185DV or Miller Multimatic 220 are popular mid-range choices for that reason.
Conclusion
Yes, you can TIG weld aluminum with DC—but it takes serious prep and a bit of patience. You’ll need to clean the surface thoroughly, preheat the metal, and control your arc carefully. The results won’t win any beauty contests, but if you’re welding thicker aluminum and just need it to hold, DC can work.
This technique is best for hobbyists and mobile welders doing the occasional repair—not for someone building aluminum projects day in and day out. For regular aluminum work, an AC/DC TIG machine is definitely worth the upgrade.