Best TIG Rod for Cast Aluminum: Top Choices for Clean, Strong Welds
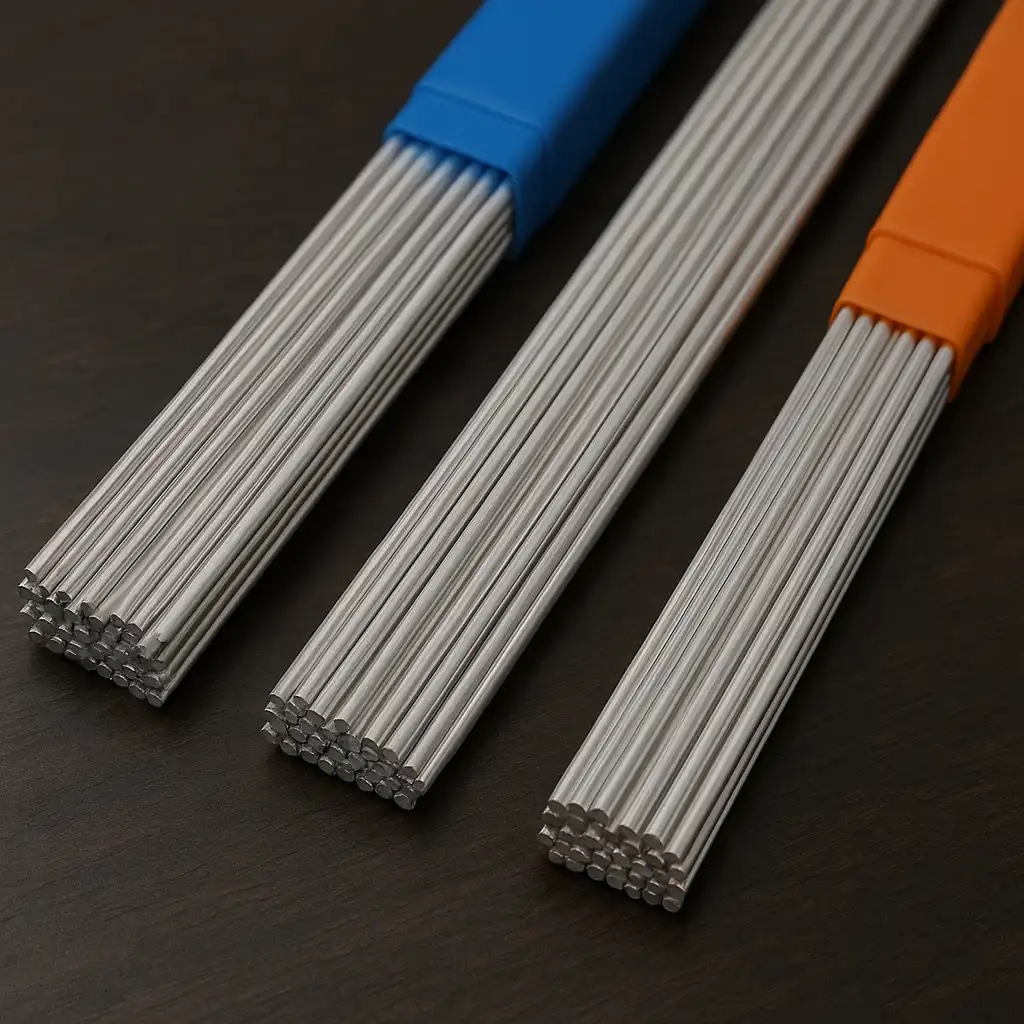
TIG welding cast aluminum requires precision, patience, and most importantly, the right filler rod. Due to aluminum’s unique properties—like high thermal conductivity and oxide formation—choosing the proper rod can make or break your weld. Whether you’re fixing a cracked casting or fabricating a custom part, selecting the best TIG rod for cast aluminum ensures both structural integrity and visual appeal.
Why Filler Rod Selection Matters for Cast Aluminum
Welding cast aluminum is more challenging than working with standard aluminum sheet or plate. Castings often have impurities, porosity, and inconsistent compositions that can make welds brittle or porous. This is where the right filler rod becomes crucial. A rod with better fluidity, lower cracking potential, and suitable alloy compatibility will dramatically improve the final result.
Blue Demon ER4943 Review
Blue Demon ER4943 rods are a solid upgrade from the common ER4043 for cast aluminum. These rods offer higher strength and better elongation, making them ideal for repairing engine components, housings, or brackets. The added silicon content improves flow, making it easier to bridge small gaps or fill porous sections without compromising strength.
EEASSA ER4047 Review
If you’re working with thin-walled castings or need a lower temperature option, the EEASSA ER4047 rods are a go-to choice. Designed with high silicon content, they melt at lower temperatures, minimizing the chance of warping or distortion. These rods also offer excellent brazing capability, useful for aluminum water tanks or HVAC parts.
ARCCAPTAIN ER4043 Review
The ARCCAPTAIN ER4043 is a well-balanced option for everyday cast aluminum welding. While it doesn’t match the strength of ER4943, it’s easier to control and produces smooth, shiny welds. This makes it perfect for beginners or when aesthetics are a top priority. It’s particularly effective on older or oxidized cast aluminum surfaces.
When to Use Each Rod
- ER4943: When strength and ductility are critical.
- ER4047: When you need lower heat input and better brazing qualities.
- ER4043: When working on general-purpose applications with a focus on ease of use and clean finishes.
Conclusion
Finding the best TIG rod for cast aluminum depends on your project’s needs—whether it’s high strength, low temperature flow, or easy usability. Each rod reviewed here serves a distinct role and helps you get the most out of your TIG welder when dealing with complex aluminum castings.