7014 vs 6013 Welding Rod: Which Stick Electrode Fits Your Job?
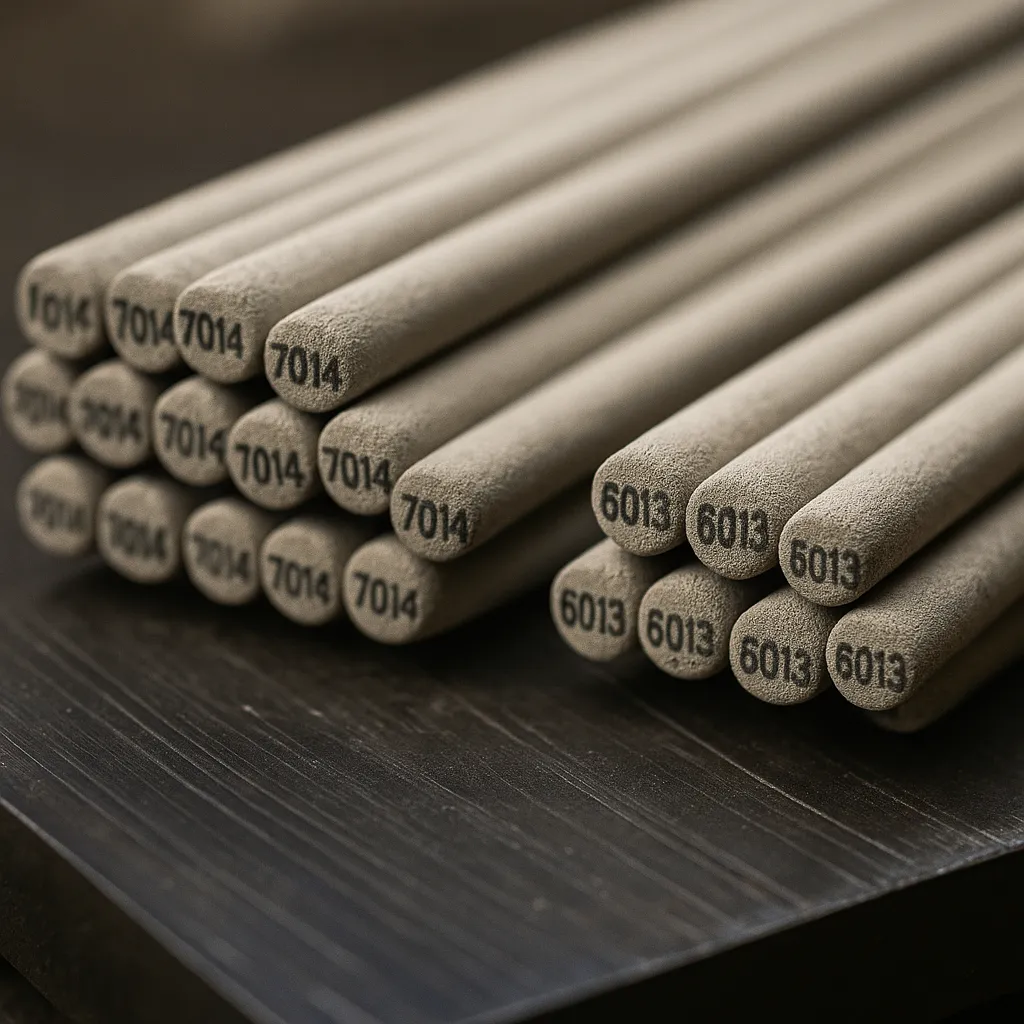
Whether you’re patching up a trailer frame or laying beads on a DIY project, choosing the right stick electrode can make all the difference. Two of the most popular options—7014 and 6013—are both reliable, easy to find, and beginner-friendly. But they perform a bit differently once you’re actually striking an arc.
Here’s a breakdown of what sets these two rods apart and when you’d want to use one over the other.
Ease of Use: Forgiving or Firm?
When it comes to user-friendliness, 6013 takes the lead—especially for new welders or those using compact machines. It lights up quickly, runs with a soft arc, and doesn’t demand much cleanup. That makes it a go-to for light fabrication, home repairs, or thin metal projects.
7014 is still beginner-friendly, but it offers a slightly more assertive arc. It runs smoother on thicker steel and produces a stronger weld if your machine can keep up. It’s a great next step for welders looking to move beyond quick patch jobs and into cleaner, more durable welds.
Arc Behavior and Weld Appearance
6013 is known for its smooth, low-penetration arc and clean finish. It’s ideal for vertical or overhead welding, especially when you want easy slag removal and minimal spatter. The weld bead is narrow and tidy, which works well on thin materials.
7014 lays down a wider bead with better penetration, thanks to its iron powder flux. The result? Welds that look more polished and professional with a bit more strength built in. It runs best in flat or horizontal positions, where it can really show off its stable arc.
Machine Compatibility and Performance
Both rods can be run on AC or DC machines, which makes them accessible for most home and shop setups. However, 6013 is a better fit for smaller 110V welders. It doesn’t need a ton of amperage to run smoothly and gives solid results even on lower-output equipment.
7014 prefers a bit more juice. It thrives with consistent amperage and does best on clean surfaces. If you’re using a 220V stick welder or have a unit with solid arc control, you’ll likely see a noticeable performance bump from switching to 7014.
Overall Value and Practical Use
For general-purpose welding, both rods offer great value. They’re affordable, dependable, and available at just about any welding supply shop or hardware store.
6013 is a smart pick if you’re doing sheet metal, ornamental iron, or farm equipment repairs. It’s simple to run and doesn’t require perfect prep. On the other hand, 7014 is better suited for heavier joints and clean surfaces—think garage fabrications, frames, or structural add-ons.
Conclusion
Both 7014 and 6013 welding rods bring something useful to the table. If you’re working on thin metal, welding overhead, or using a low-amp welder, 6013 is a safe and forgiving bet. But if you’re after stronger welds, better bead appearance, and you’ve got the machine to power it, 7014 is the way to go. Many welders keep both rods in their kit—because sometimes, the right answer is having options.