Most Common Aluminum Filler Rods Explained for Everyday Welders
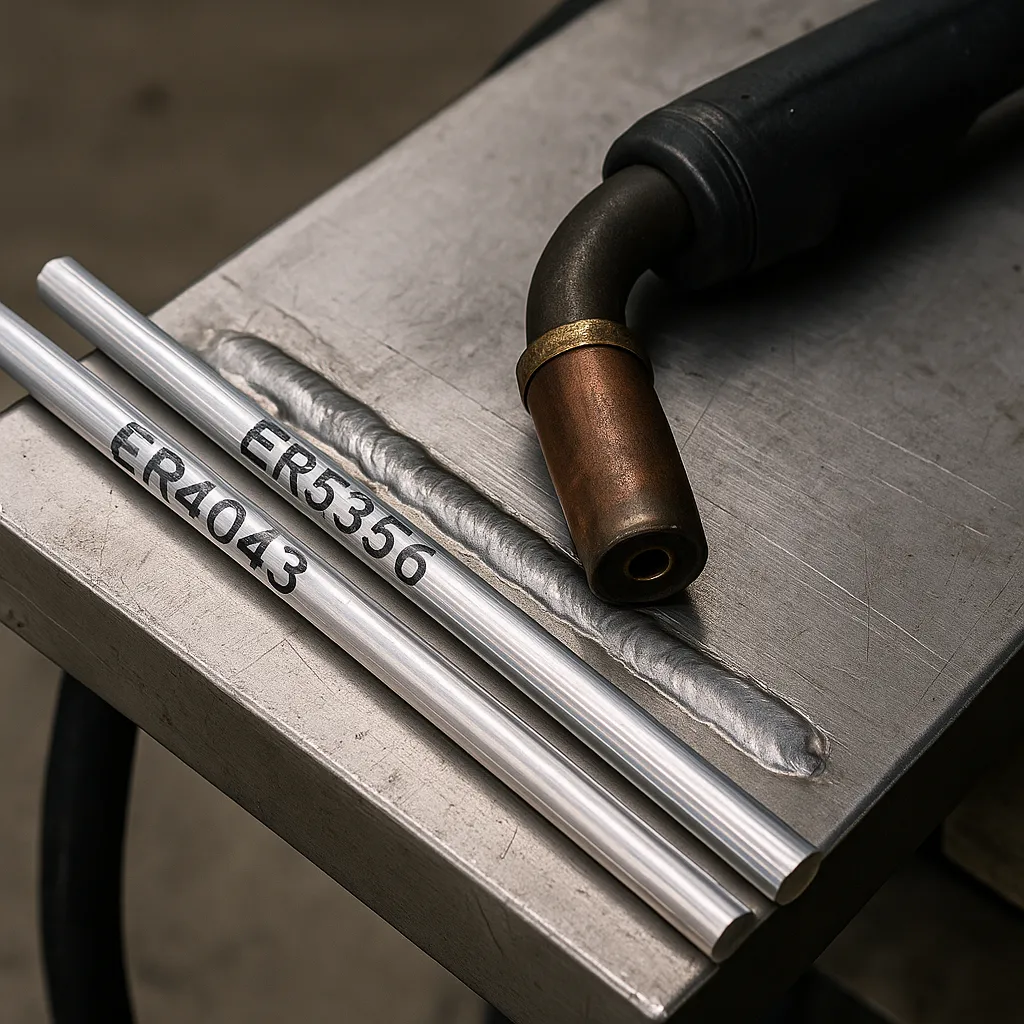
Disclosure: This post contains affiliate links. As an Amazon Associate, I earn from qualifying purchases—at no extra cost to you.
Aluminum welding is its own beast—but knowing the right filler rod can save you a ton of time and headaches. Whether you’re working on 6061 tubing, boat repairs, or general fabrication, the rod you choose makes a big difference in strength, flow, and finish.
The two rods that come up again and again in welding shops and forums are ER4043 and ER5356. They’re not just popular—they’re the go-to options for different types of aluminum work. Let’s break down what makes each one stand out and how to pick the right one for your next project.
ER4043: Smooth Flow, Forgiving to Use
ER4043 is widely known for its smooth puddle and ease of control. It contains silicon, which helps the filler flow more easily and reduces the risk of cracking—especially helpful when you’re welding heat-treated alloys like 6061.
Most welders prefer ER4043 for general jobs like aluminum sheet, tubing, or casting repairs. It performs best when you’re joining similar grades like 6061 to 6061 or 3003.
It’s not the strongest rod on the market, but it’s consistent, and the finish is clean. That makes it ideal for parts where cosmetics matter—think visible welds on toolboxes or lightweight frames.
ER5356: Stronger Welds, Tougher Conditions
If you’re welding something that’s going to take abuse—like trailers, boats, or outdoor equipment—ER5356 is the filler rod most welders turn to. It has higher tensile strength and better corrosion resistance compared to ER4043.
This rod pairs well with 5XXX series alloys like 5052 and is also a solid match for 6061 in structural applications. However, it’s less forgiving than ER4043 and requires a cleaner base material and tighter technique to avoid porosity or cracking.
Many professionals prefer ER5356 when performance matters more than ease of use. It’s also a better choice if your welds will be anodized, since ER4043 can discolor under that finish.
Choosing the Right Rod for the Job
Your decision really comes down to the job at hand. For clean aluminum work that’s not highly structural—like patching up a ladder or working on car panels—ER4043 gets it done with minimal fuss.
On the other hand, if you’re fabricating something load-bearing or working in marine environments, the added strength and resistance of ER5356 makes it the smarter choice.
According to user feedback and welding community threads, many hobby welders start with ER4043 and gradually move to ER5356 as they get more comfortable managing arc control and travel speed.
Conclusion
ER4043 and ER5356 are the most common aluminum filler rods for good reason. ER4043 is easy to run, great for clean looks, and perfect for light-duty projects. ER5356 brings extra strength and durability, making it ideal for structural work or tough environments. Match your rod to the alloy and job type, and you’ll get stronger, cleaner results no matter what’s on your bench.