7014 vs 7018 Welding Rods: Which One’s Right for Your Next Project?
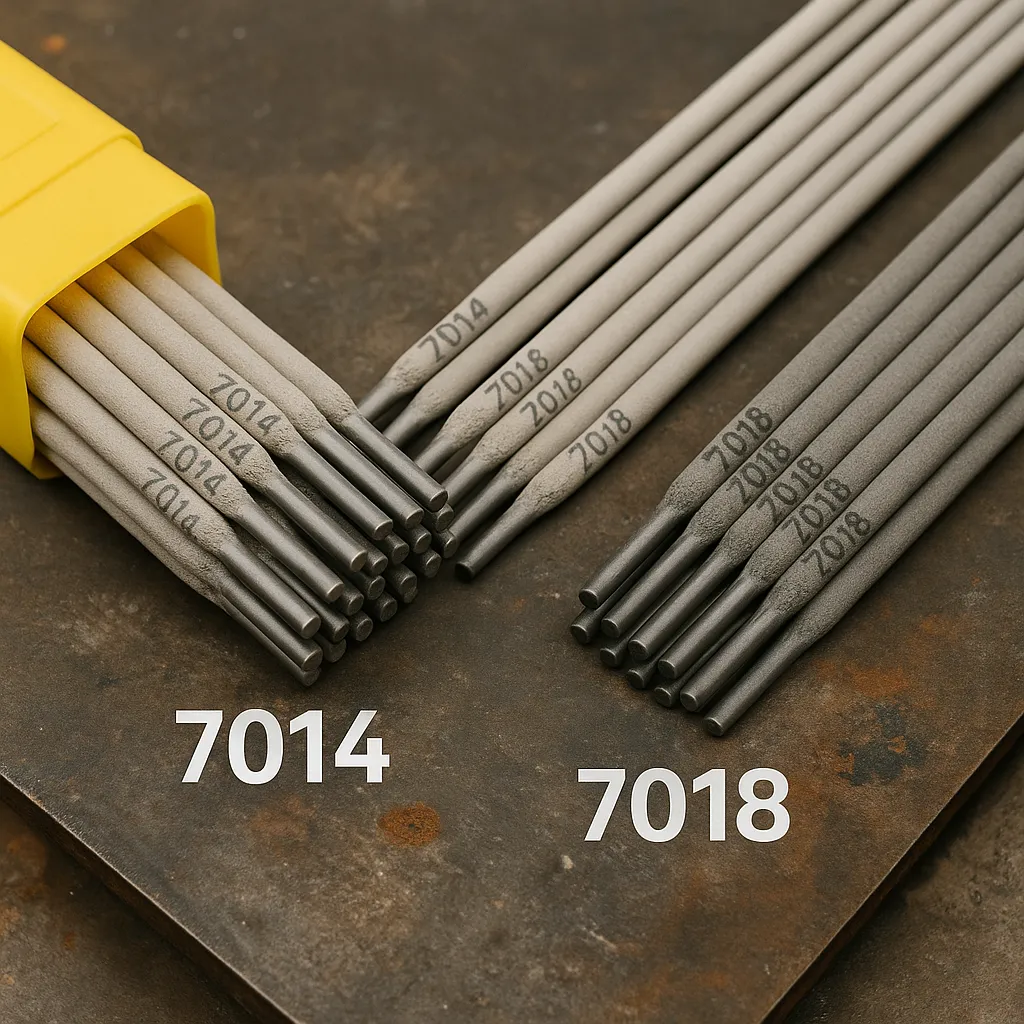
Disclosure: This post contains affiliate links. As an Amazon Associate, I earn from qualifying purchases—at no extra cost to you.
When it comes to stick welding mild steel, 7014 and 7018 rods are two of the most common options you’ll run into. Each has its strengths, and the right choice depends on your setup, welding goals, and the kind of results you’re aiming for.
Let’s take a closer look at how these two rods compare where it really counts—on the arc and in the shop.
Arc Feel and Bead Results
7018 is known for its smooth, steady arc and clean, low-spatter welds. It’s often used in structural work because it produces strong, professional-looking beads that hold up under pressure. Based on welder reviews and jobsite feedback, many prefer 7018 for its crisp finish and solid penetration on thicker steel.
7014, on the other hand, runs a bit hotter and deposits metal quickly. Its arc is a little more aggressive, but it still creates a solid bead—especially on flat or horizontal joints. It doesn’t offer quite the same finesse as 7018, but it’s dependable for general-purpose welding and gets the job done without much fuss.
Compatibility with Welders
7014 is more forgiving when it comes to machine requirements. It works well with AC, DC+, or DC– setups and doesn’t need a high open-circuit voltage. That makes it a great fit for hobby welders using small AC machines or older buzz boxes.
7018 typically runs best on AC or DC+ and benefits from a welder with steady arc control. If you’re using a low-voltage machine, consider 7018AC—a version designed to handle less-than-ideal power sources. This rod is a favorite for those with inverter welders or more advanced gear.
For weekend projects in a home garage, 7014 often makes things easier. If you’re set up for heavier-duty work or chasing certification, 7018 gives you more long-term versatility.
Learning Curve and Ease of Use
7014 is popular with beginners for good reason. It’s easy to strike and restart, and the slag usually chips off with minimal effort. According to user reports, it’s more forgiving if your technique isn’t perfect—making it a great training rod or everyday option for quick repairs.
7018 takes a bit more skill. The arc is smoother, but the rod can be harder to restart if it cools. It also needs to be stored dry or reconditioned before use, as moisture can lead to weld defects. While it may take more practice, many welders agree the payoff is worth it once you’ve got it dialed in.
Strength and Application
Both rods have a tensile strength of 70,000 psi, but they’re not used interchangeably. 7018 is a low-hydrogen rod, which makes it better for critical joints, load-bearing welds, and code-compliant work. You’ll find it everywhere from structural steel jobs to pipe welding.
7014 doesn’t offer the same hydrogen protection, but it’s strong enough for many non-code projects like equipment repairs, gates, frames, and hobby builds.
If you’re doing work that needs to pass inspection or carry a load, go with 7018. For everything else, 7014 is a reliable alternative with less prep and fuss.
Conclusion
7014 and 7018 are both solid stick welding rods, but they’re suited for different situations. 7014 is a great pick for beginners or anyone using a basic AC welder—it’s easy to strike, forgiving on technique, and ideal for general repairs or light fabrication. On the other hand, 7018 is built for strength and durability, offering low-hydrogen welds that meet structural standards. If your machine can handle it and you’re aiming for clean, strong welds on critical joints, 7018 is the rod to learn.