What Is TIG Welding? Mastering the Cleanest Welding Method
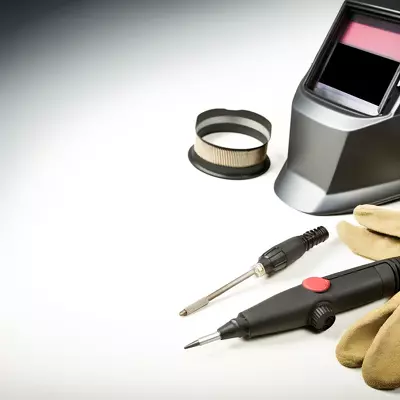
Disclosure: This post contains affiliate links. As an Amazon Associate, I earn from qualifying purchases—at no extra cost to you.
TIG welding—also known as Tungsten Inert Gas welding—is widely recognized for its precision and clean results. It’s a top choice when your project demands an attractive finish or involves tricky materials like aluminum or stainless steel. From bike frames to custom kitchen fixtures, TIG is the method many pros turn to when they need the job done right.
Let’s look at what makes TIG welding unique, what gear you’ll need, and where it really shines.
It Offers Precision, but Takes Practice
TIG welding gives you full control over heat, filler material, and arc. You’ll hold the torch in one hand and manually feed a filler rod with the other, while managing amperage—often with a foot pedal. This process demands good coordination and patience, especially when you’re just starting out.
Many welders on forums mention that once you get the hang of TIG, it becomes second nature. The payoff? Incredibly smooth, precise welds with minimal cleanup.
Best for Thin Metals and Clean, Visible Welds
Where TIG really proves itself is on thin materials or projects where the final look matters. It’s especially popular for:
- Stainless steel countertops and fixtures
- Aluminum bike frames and marine components
- Automotive exhaust systems and trim
- Artistic metalwork and clean corner joints
Because TIG doesn’t spatter and lets you control every aspect of the weld, it’s ideal for visible surfaces or delicate parts. You can avoid burning through thin sheet metal, and you often won’t need to grind or polish afterward.
Setup Is More Involved, but Gear Has Improved
TIG welding does require a more involved setup compared to stick or MIG. Based on user reviews and manufacturer guides, here’s what you’ll need:
- A TIG-capable welder (preferably with AC/DC options)
- High-quality tungsten electrodes
- A cylinder of 100% argon gas
- Matched filler rods for your base metal
- Either a foot pedal or fingertip control for amperage
Fortunately, newer machines with digital controls and high-frequency arc starting are making things more beginner-friendly. Many small shop welders say these upgrades helped them get more consistent welds faster.
Safety and Comfort Are Key for Long TIG Sessions
TIG welding doesn’t create much spatter or slag, but it still demands focus and proper gear. Since you’re usually working up close and dealing with intense light, good protection is essential.
To stay safe and comfortable:
- Use a reliable auto-darkening helmet with high optical clarity
- Choose flexible TIG gloves to improve dexterity
- Wear a lightweight, flame-resistant jacket
- Set up good lighting and ventilation, especially when working indoors
Comfort isn’t just a bonus—it actually helps you control the weld better, especially on long or detailed jobs.
Conclusion
TIG welding delivers unmatched weld quality, especially when working with thin or delicate materials. It’s slower and requires more finesse than MIG or stick, but it rewards you with clean, precise results that look great right off the torch.
Pros: Incredible control, no spatter, clean welds
Cons: Steep learning curve, more gear to manage, slower process
Best for: Aluminum, stainless, thin sheet metal, and decorative projects
If you enjoy fine-tuning your skills and want pro-level results, TIG is worth investing the time and tools. For fast fabrication or structural repairs, MIG or stick might be the more practical route.