What Filler Rod for Aluminum: Choose the Right Rod for Strong, Clean Welds
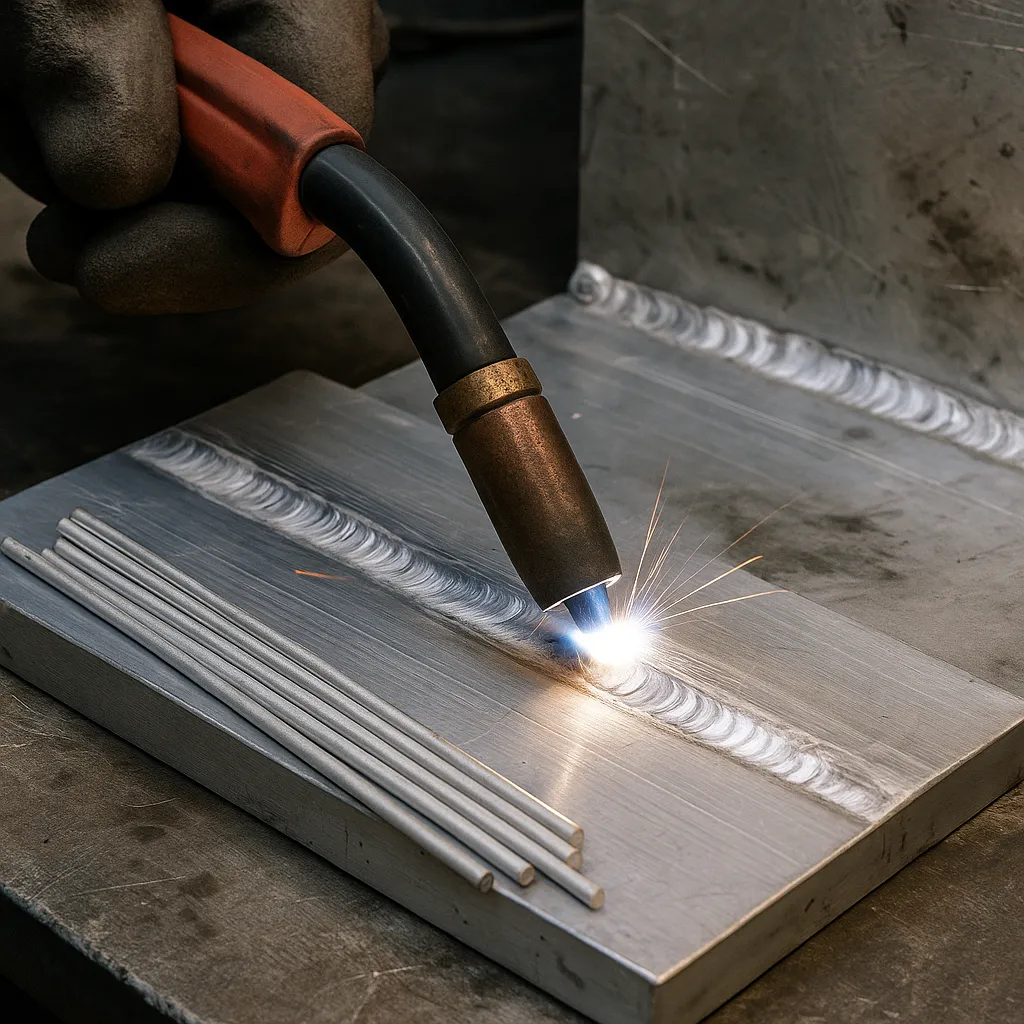
Disclosure: This post contains affiliate links. As an Amazon Associate, I earn from qualifying purchases—at no extra cost to you.
Welding aluminum isn’t quite the same as working with steel. It’s more sensitive to contamination, more prone to warping, and it demands the right filler rod to get solid, long-lasting results. If you’re using the wrong rod—even with a flawless technique—you could end up with weak joints or cracks down the line.
Let’s break down which filler rods work best with aluminum and why your choice really matters.
ER4043 vs ER5356: The Two Most Popular Picks
When it comes to aluminum filler rods, ER4043 and ER5356 dominate the scene. They both have solid reputations, but they serve slightly different purposes.
ER4043 is known for its smooth arc and excellent flow. It contains silicon, which helps the weld puddle spread easily and reduces the chance of hot cracking. Many welders—especially those using TIG—prefer it for jobs that require a clean finish and minimal spatter. It’s commonly paired with 6061 aluminum and similar alloys.
ER5356, on the other hand, is a magnesium-bearing rod with higher tensile strength. It’s often chosen for structural applications where strength and ductility matter more than appearance. It’s not quite as fluid as ER4043, so it may take a little more finesse, especially with thinner material.
Based on user reviews and community feedback, ER4043 is easier for beginners to handle, while ER5356 offers more durability once your technique is dialed in.
Match Your Filler Rod to the Aluminum Alloy
Not all aluminum is created equal, and your base metal should guide your filler rod choice.
- 6061 aluminum works well with ER4043 for most general tasks. But if you’re after more strength or doing MIG work, ER5356 is a better match.
- 5052 aluminum usually requires ER5356 for optimal weld strength and corrosion resistance.
- Avoid mixing silicon and magnesium-based fillers without checking compatibility charts—some combinations can lead to poor weld integrity or cracking.
For best results, always verify the alloy and double-check filler recommendations before firing up your welder.
Ease of Use and Weld Appearance
If you’re still getting the hang of TIG welding or working on smaller, cosmetic jobs, ER4043 will likely be your friend. It’s more forgiving of minor mistakes, flows better, and gives you a nice, smooth bead. It also handles slightly contaminated base metal better than ER5356.
ER5356, while stronger, requires tighter joint prep and cleaner conditions. It can leave a slightly rougher appearance if you’re not used to running it. That said, it holds up better in structural or marine environments.
Feedability and Setup Considerations
If you’re MIG welding with a spool gun or push-pull system, ER5356 tends to feed more reliably thanks to its stiffer wire. ER4043 is softer and can bird-nest in some setups unless your tension and liner are dialed in just right.
For TIG welding, both rods are solid choices and will work well with standard AC TIG machines. Just be sure to keep your tungsten clean and sharp, especially with aluminum’s oxide layer in the mix.
Conclusion
When it comes to aluminum welding, the filler rod you choose matters. ER4043 is easy to run, lays down a clean bead, and works great for general-purpose TIG jobs—especially if you’re using 6061 aluminum. ER5356 delivers more strength and durability, making it ideal for MIG welding, structural work, or applications exposed to harsh conditions. If you’re new to aluminum or focusing on precision, go with ER4043. For tougher tasks where strength is key, ER5356 is the way to go.