TIG Welding with Silicon Bronze: A Versatile Brazing Solution
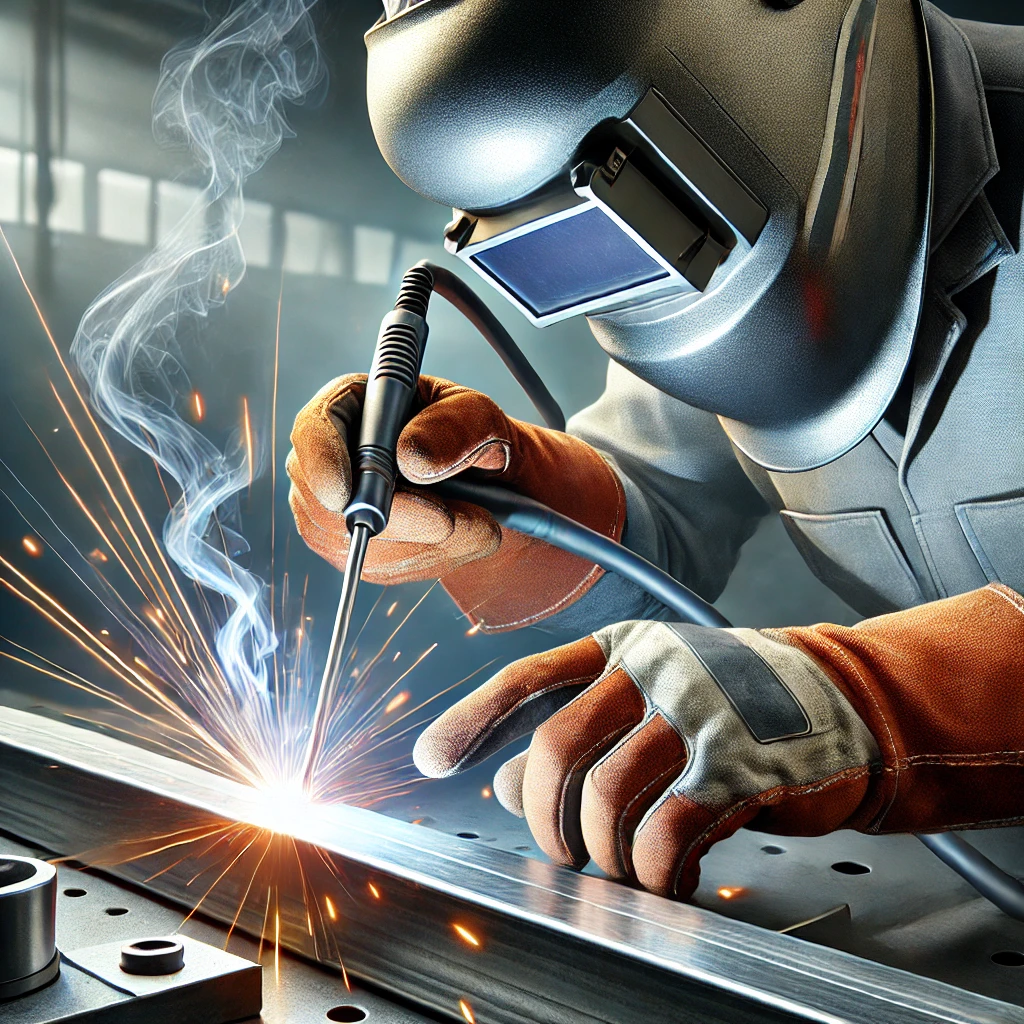
Understanding TIG Welding with Silicon Bronze
TIG welding with silicon bronze is a popular method for joining dissimilar metals, reducing heat input, and preventing warping. Due to its low melting point and excellent corrosion resistance, this technique is commonly applied in automotive restoration, artistic metalwork, and sheet metal fabrication.
Advantages of TIG Welding with Silicon Bronze
- Low Heat Input – Helps prevent warping and distortion, especially on thin metals.
- Great for Dissimilar Metals – Works well for joining copper, brass, stainless steel, and even cast iron.
- Corrosion Resistance – Silicon bronze provides excellent resistance against corrosion, making it ideal for marine and outdoor applications.
- Aesthetic Finish – Offers a clean, smooth weld bead that blends well with artistic and decorative projects.
Best Applications for Silicon Bronze
Automotive and Restoration Work
- Ideal for body panels and patchwork without causing excessive heat damage.
- Works well for filling gaps in rusted or worn-out metal sections.
Artistic and Decorative Metalwork
- Preferred by sculptors and designers for its clean appearance.
- Commonly used for crafting furniture, gates, and ornamental structures.
Sheet Metal and Thin Materials
- Provides strong joints with minimal distortion.
- Useful in HVAC applications, roofing, and ductwork repairs.
Proper Techniques for TIG Welding with Silicon Bronze
Choosing the Right Tungsten Electrode
- Use pure tungsten (green) or 2% lanthanated tungsten (blue) for stable arc performance.
- Maintain a sharp point to ensure precision and control.
Shielding Gas Selection
- 100% Argon is recommended for optimal weld quality.
- Avoid helium-based mixtures, as they may cause excessive heat.
Proper Heat Control
- Keep the amperage lower than traditional TIG welding to prevent burn-through.
- Work with short bursts rather than continuous welding for better control.
Filler Rod Selection
- Use ERCuSi-A (Silicon Bronze) filler rod for strong, durable joints.
- Clean the base metal thoroughly to remove oxidation and contaminants before welding.
Common Challenges and Solutions
- Porosity Issues – Ensure the metal surface is clean and free of oil, grease, and oxidation.
- Weak Welds on Steel – Since silicon bronze forms a brazed joint rather than a fusion weld, mechanical support may be required.
- Arc Blow – Adjust gas flow and tungsten angle to maintain arc stability.
Conclusion
TIG welding with silicon bronze is a versatile process that allows for low-heat joining of various metals while maintaining structural integrity. Whether working on automotive restorations, artistic sculptures, or industrial applications, this method offers a balance of strength, corrosion resistance, and aesthetic appeal.