Does Stick Welding Require Gas? A Practical Guide for Beginners
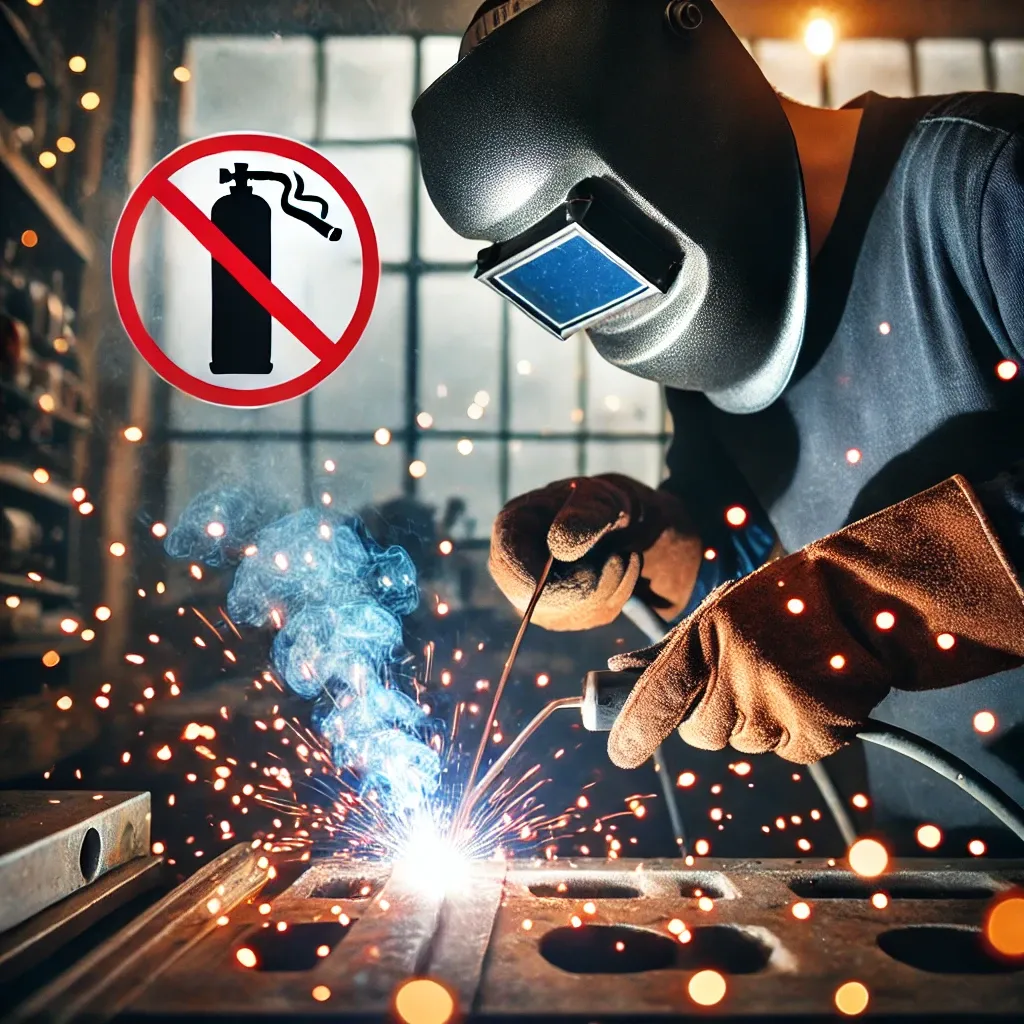
Disclosure: This post contains affiliate links. As an Amazon Associate, I earn from qualifying purchases—at no extra cost to you.
When you’re welding outdoors or setting up a small garage project, the last thing you want is to drag around a bulky gas cylinder. That’s where stick welding (also known as Shielded Metal Arc Welding or SMAW) shines. It doesn’t rely on bottled gas like MIG or TIG welding. Instead, it creates its own shielding as you work, keeping things simple and portable.
If you’re wondering how that works—or why so many welders still choose stick for repairs, farm jobs, and structural work—this guide breaks it down using real-world advice from welders who use stick setups every day.
How to Use Stick Welding Shields Without Gas
Unlike MIG or TIG welding, stick welding doesn’t need a gas tank. The electrode itself is coated in flux. As the rod burns, the flux melts and forms a protective gas cloud around the weld pool. This shields your weld from oxygen and moisture in the air. At the same time, molten slag forms over the weld to keep contaminants out as it cools.
Based on welder feedback from forums and small shops, this self-shielding process is one of stick welding’s biggest advantages. It’s why welders can work outdoors, even in windy conditions, without worrying about losing gas coverage or carrying heavy cylinders.
Easy Setup and True Portability
Stick welding setups are simple. You won’t need gas bottles, hoses, or regulators. Many small shop welders mention that setting up a stick welder is as easy as connecting the electrode holder, ground clamp, and flipping the machine on.
Because there’s no gas equipment to manage, stick welders are easy to transport. Many portable inverter machines weigh less than 20 pounds, making them ideal for field repairs, farm jobs, and worksite welding. Small garage welders often say this simplicity and portability were key reasons they chose stick as their first welding process.
Learning Curve and Arc Control
While stick welding setup is simple, using it takes practice. Holding the correct arc length and managing slag buildup can be tricky for beginners. According to welder feedback from user forums, many new welders find starting and maintaining the arc difficult at first.
Modern inverter stick welders help reduce frustration. Features like hot start and arc force provide a smoother arc and prevent sticking. Once you get used to controlling the arc, stick welding becomes a reliable method for small repairs, metal fabrication, and structural welding projects.
Safety and Long-Term Value
Since stick welding doesn’t require gas tanks, you avoid the risks that come with pressurized cylinders. However, stick welding produces more spatter, fumes, and slag compared to MIG or TIG. Proper ventilation, a quality welding helmet, and protective gear are still essential.
In terms of value, stick welders are affordable and built to last. Many welders report using their basic stick machines for years without major maintenance. With fewer components like gas regulators and hoses, you’ll spend less on upkeep and replacement parts.
Conclusion
So, does stick welding require gas? No. Stick welders use flux-coated electrodes that create their own shielding, making gas cylinders unnecessary. This makes stick welding simple to set up, portable, and ideal for outdoor work. While there’s a learning curve and more cleanup compared to MIG or TIG, many welders appreciate the practicality and durability of stick setups—whether they’re working in a garage, a farm, or a mobile repair business.