Can You Weld Titanium to Steel? Smart Tips Before You Start
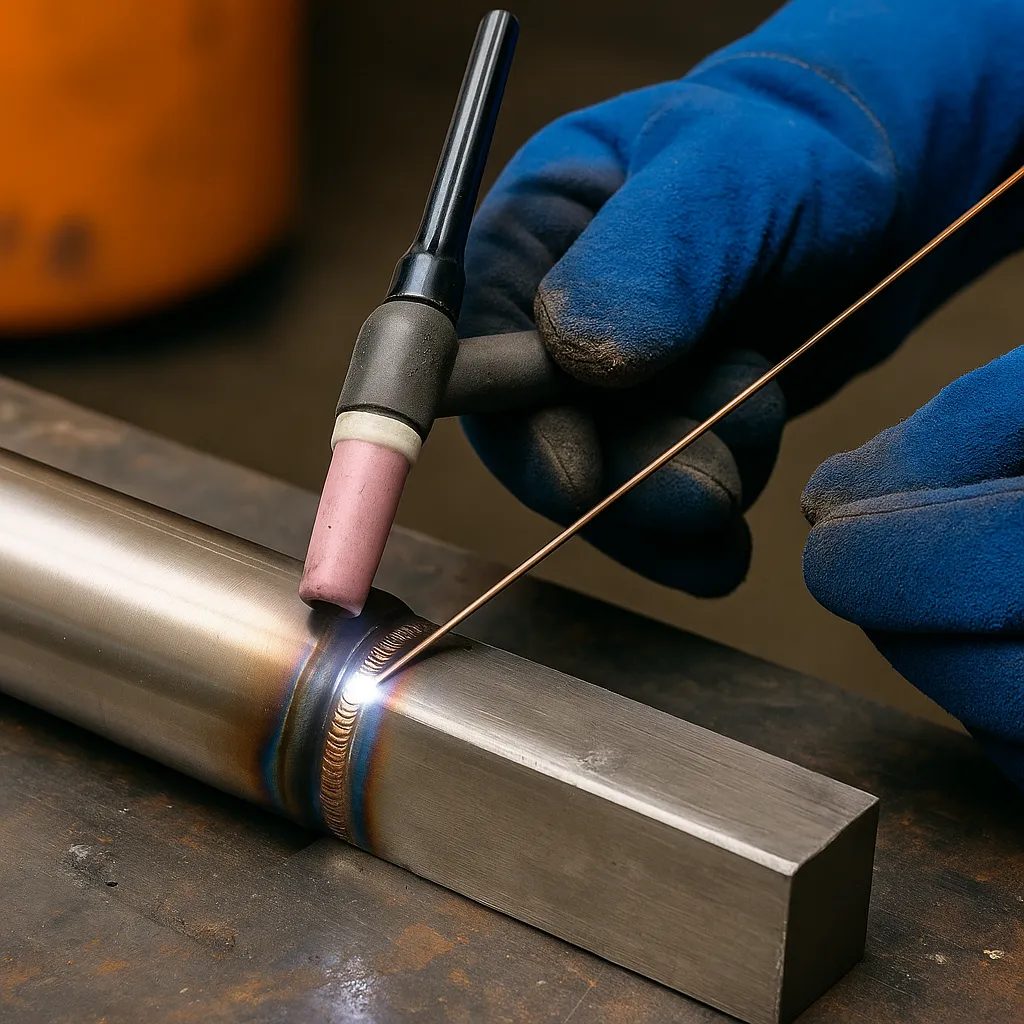
Disclosure: This post contains affiliate links. As an Amazon Associate, I earn from qualifying purchases—at no extra cost to you.
Welding titanium to steel is one of those jobs that sounds simple—until you try it. These metals might both be strong, but they’re not naturally compatible. You can’t just fuse them together with your average TIG welder and expect a clean result.
Still, with the right process and some careful planning, it is possible. Let’s break down why it’s tricky, what methods actually work, and what real welders have learned along the way.
Why Titanium and Steel Don’t Mix Easily
Titanium and steel have very different chemical properties. When welded directly, titanium tends to absorb carbon and iron from steel, forming brittle compounds that crack under stress. Their thermal expansion rates also don’t match, which puts extra strain on the weld as it cools.
According to feedback from experienced fabricators and welding forums, you’ll almost always need an interlayer, like nickel or vanadium. That buffer helps keep the metals from reacting directly with each other, creating a more stable joint.
Which Welding Methods Actually Work?
Traditional welding techniques like MIG or TIG aren’t ideal for this job. Most successful welds between titanium and steel are done using explosion welding or diffusion bonding, both of which rely on pressure rather than a molten pool.
That said, advanced TIG setups have been used in controlled lab environments. These require ultra-clean prep, separate brushes for each metal, high-purity shielding gas, and exact heat control. Even then, results can be hit or miss without the right interlayer.
Equipment, Setup, and Safety Concerns
Working with titanium brings added safety concerns. If it’s overheated or poorly shielded, titanium can ignite, leading to a fire that’s tough to extinguish. That’s why most small shops avoid titanium unless they’re properly equipped.
Based on welder reviews and user videos, many hobbyists recommend mechanical fastening as a safer and more practical alternative. It’s more predictable and doesn’t require specialized gear. For structural jobs where strength is critical, it’s best to leave titanium-to-steel welding to professional fabricators.
Is It Worth It for DIY Welders?
For most weekend welders or small shop projects, probably not. The materials are expensive, the process is complex, and the margin for error is small. Unless you’re working on aerospace parts or specialized manufacturing, you’re better off finding another approach.
If you’re just exploring the idea, start by researching transition joints or exploring how pros handle it with interlayers and post-weld treatments. That way, you’ll know what you’re getting into before you spend time or money chasing a tough weld.
Conclusion
Welding titanium to steel is possible—but it’s not easy, cheap, or beginner-friendly.
- Direct welds don’t hold up without an interlayer
- Explosion welding and diffusion bonding work best
- Shielding, prep, and safety are more demanding than usual
- Alternatives like mechanical joints are safer and more practical for most welders
If you’re serious about trying it, plan carefully and know the risks—or consider outsourcing the job to someone with the right tools and experience.