Can All Metals Be Welded Together? Challenges and Solutions
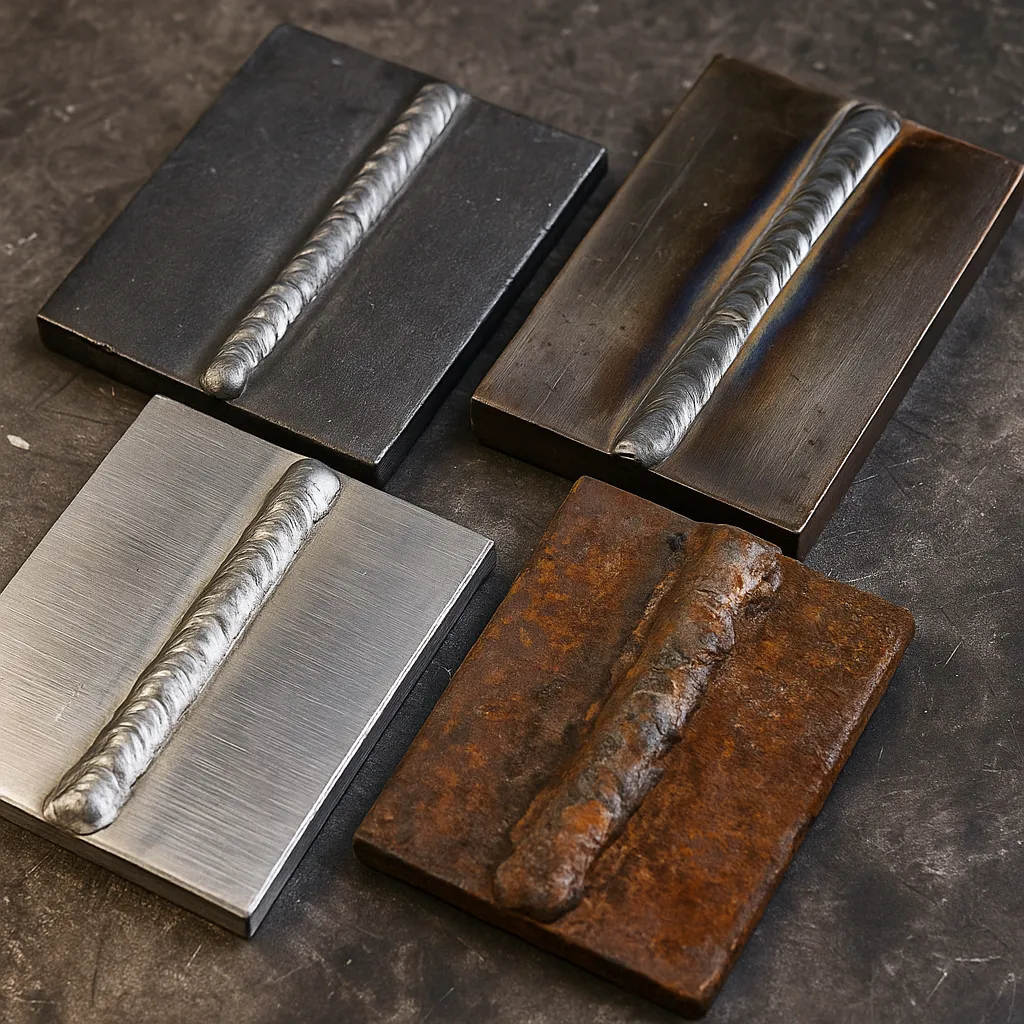
Disclosure: This post contains affiliate links. As an Amazon Associate, I earn from qualifying purchases—at no extra cost to you.
Welding is a powerful skill, but not every metal responds well to heat and filler. Some weld up clean and smooth, while others crack, warp, or just won’t bond without specialized gear. Whether you’re building a firepit in your backyard or repairing a trailer in your garage, knowing what metals can be welded—and how—is key to saving time, materials, and frustration.
Let’s break it all down in plain terms.
Mild Steel: The Go-To for a Reason
Mild steel is the most beginner-friendly metal out there. It’s cheap, widely available, and works great with MIG, stick, or flux-core welders—even basic ones.
It has low carbon content, which makes it less brittle and more forgiving. According to plenty of beginner welders, it delivers steady arc performance and doesn’t require a fancy machine to get decent results. ER70S-6 wire and a 75/25 gas mix are usually enough for clean, reliable welds.
If you’re welding table legs, gates, or brackets, mild steel is your easiest starting point.
Stainless Steel: Great Results if You Prep Right
Stainless steel can absolutely be welded—but it takes a bit more care. It holds heat longer than mild steel, which means it can warp if you’re not managing your heat input.
Many hobby welders report success using a MIG welder with the right stainless wire and a tri-mix shielding gas. For cleaner results—especially on thinner stainless—TIG welding is usually the better choice. Just make sure to match your filler rod to your base metal (308L for 304 stainless is a common pair).
Stainless looks sharp and resists rust, but it’s less forgiving than mild steel—plan your setup accordingly.
Aluminum: Lightweight but Demanding
Aluminum is weldable, but it takes practice and the right equipment. Because it conducts heat so quickly, puddle control is a real challenge.
According to feedback from welding forums and video tutorials, most hobbyists get better results using AC TIG machines or spool gun MIG setups. Pre-cleaning the metal with a stainless brush and moving quickly makes a big difference.
Aluminum’s popular for trailers, outdoor gear, and even bike frames—but don’t be discouraged if your first few beads aren’t pretty.
Cast Iron, Titanium, and Others: Possible, But Specialized
Some metals are weldable, but they need a specific approach—and often advanced gear.
Cast iron is brittle and often cracks unless preheated and cooled slowly. A nickel-based rod is typically recommended, or in many cases, brazing is used instead.
Titanium can be welded but is extremely reactive to air. It requires high-purity argon shielding and a perfectly clean environment—usually found only in pro shops.
Galvanized steel is another one to approach carefully. The zinc coating produces toxic fumes when welded, so it’s essential to grind it off first and wear proper ventilation or respiratory protection.
Other metals—like magnesium, bronze, and brass—have unique characteristics. They’re technically weldable but come with their own risks, so do your research before attempting a project.
Conclusion
Most metals can be welded—but that doesn’t mean all of them are easy. Mild steel is the best place to start if you’re new, thanks to its low cost and forgiving nature. Stainless and aluminum are a bit trickier but still within reach with the right setup. Specialty metals like cast iron and titanium? They require patience, prep, and sometimes pro-level tools.
Easier to weld:
- Mild steel (ideal for beginners)
- Stainless steel (requires prep but manageable)
- Aluminum (challenging, but learnable)
Takes experience or specialized tools:
- Cast iron
- Titanium
- Galvanized steel (remove coating and ventilate)
Start with what’s simple and work your way up. The more you weld, the better you’ll understand how each metal reacts—and which ones are worth the effort.