How to Maintain Your Welding Equipment Like a Pro: Simple Steps That Make a Big Difference
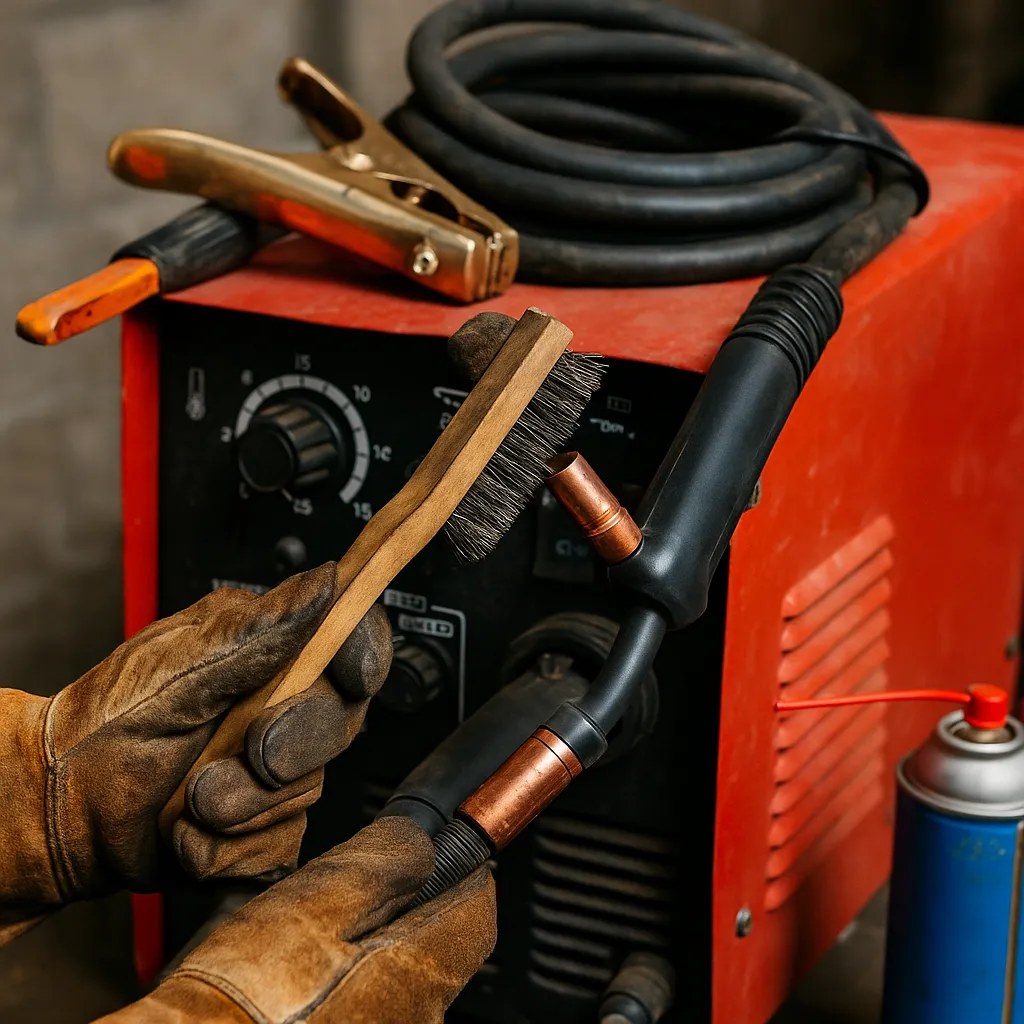
Disclosure: This post contains affiliate links. As an Amazon Associate, I earn from qualifying purchases—at no extra cost to you.
Welding gear takes a beating—between the heat, slag, dust, and day-to-day handling, it doesn’t take long for things to start slipping. If your arc feels off or your welds aren’t as clean as they used to be, your machine might just need some TLC.
Regular maintenance doesn’t have to be complicated or time-consuming. In fact, just a few simple habits can keep your setup running smoother, longer, and safer—whether you’re welding in a small garage or a side hustle shop.
Keep Your Tools Clean and Your Arc Stable
When your gear’s dirty, your welds usually suffer. Spatter buildup on the torch, dust around vents, and gunked-up tips are all common reasons for weak arcs and erratic performance.
Wipe down your torch, stinger, or MIG gun after every session. Knock off spatter, clear out the nozzle, and inspect contact tips for damage. For stick welders, clean up the electrode holder and make sure there’s no slag stuck where it shouldn’t be.
If you’re welding in a dusty environment, toss a cover over your machine when you’re done for the day. It’ll help protect the internal components from grime and moisture.
Inspect Cables and Clamps Weekly
Cables get dragged, kinked, stepped on—you name it. And over time, all that wear and tear can lead to inconsistent performance or even safety hazards.
Many hobbyists and shop welders recommend doing a quick cable inspection once a week. Look for cracks, frays, or loose connectors—especially near the ground clamp or where the cable enters the machine. Make sure your ground clamp is clean and biting down tight.
Bad connections often lead to arc instability, heat loss, and even frustrating troubleshooting sessions that could’ve been avoided with a 2-minute check.
Replace Worn Consumables and Keep Filler Rods Dry
Welding consumables wear down quickly. Contact tips, nozzles, gas diffusers—they all play a role in arc stability and wire flow. If your welds start looking off or your wire feed isn’t smooth, chances are you’ve got a worn part in the mix.
Keep spares handy and swap them out as soon as you notice wear. Also, store your stick electrodes and TIG rods in a sealed container to keep out moisture. Damp filler metal causes porosity and weak welds—something you don’t want to discover after the job’s done.
Community feedback from welding forums often points to overlooked consumables as the hidden cause of poor weld quality.
Don’t Forget Internal Cleanup and Gas Checks
You might not think about it much, but the inside of your welder collects dust and debris over time. According to manufacturer recommendations, blowing out your machine with compressed air (while it’s off and unplugged) every couple of weeks can help prevent fan issues and heat buildup.
It’s also a good idea to check your shielding gas setup. Loose fittings, cracked hoses, or leaks around the regulator can waste gas and lead to poor weld coverage. If you suspect a leak, use soapy water around the joints to spot bubbling.
Small problems here can show up as messy welds, especially if you’re working with MIG or TIG.
Conclusion
A little maintenance goes a long way in welding. Staying on top of your gear doesn’t just extend its life—it keeps your welds cleaner, your arcs more stable, and your workspace safer.
What it helps with:
- More consistent arc performance
- Longer machine and consumable lifespan
- Fewer breakdowns or frustrating weld issues
What to keep an eye on:
- Damaged leads and connectors
- Dirty or worn consumables
- Dusty internals and gas leaks
Spend a few minutes after each job checking things over. It’ll save you time, money, and a whole lot of aggravation in the long run.