What 7018 Welding Rod Really Means (And Why It Matters)
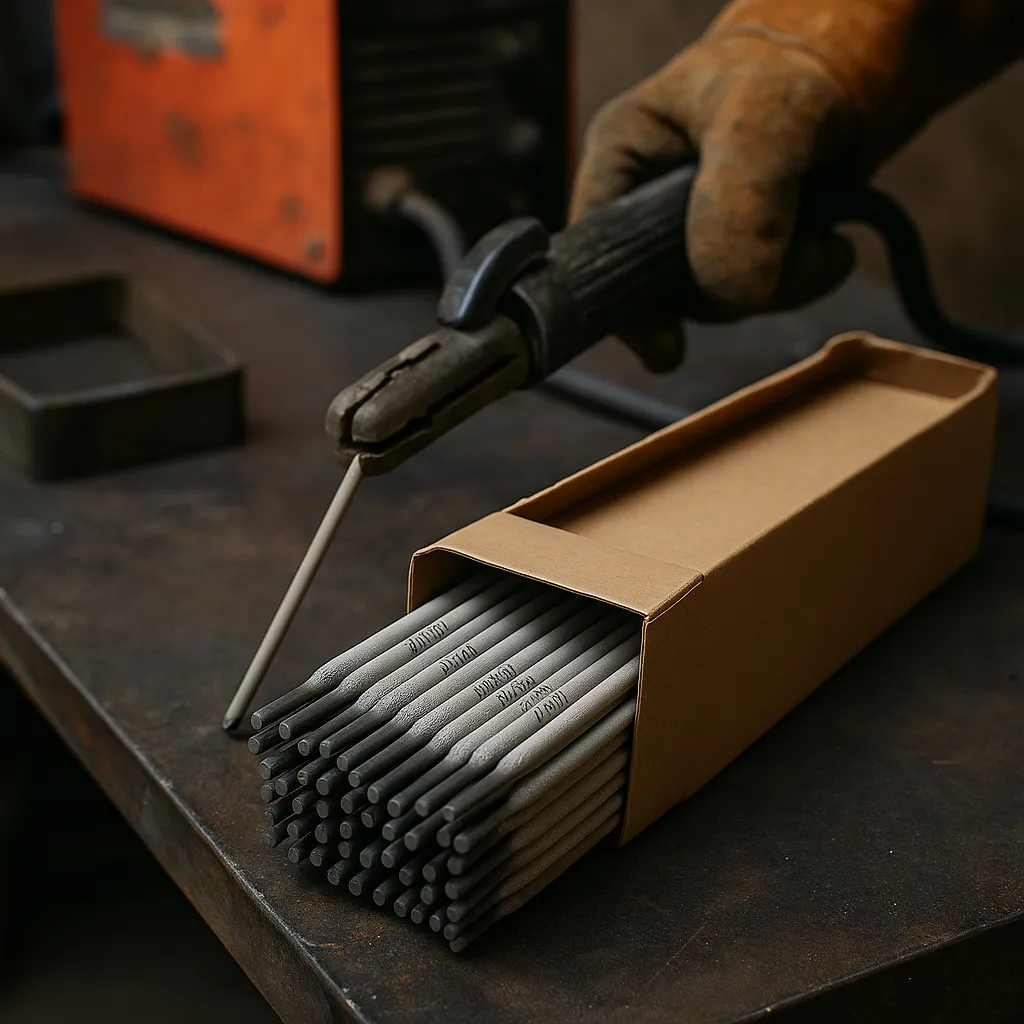
The 7018 welding rod is a staple in the welding world—well-known for its strength, clean welds, and low-hydrogen properties. Whether you’re patching up a rusty trailer or working on structural beams, this rod comes up again and again as a reliable choice.
Let’s break down what those four digits actually mean and how this rod performs when you strike an arc in real-world scenarios.
Breaking Down the Numbers
Each number in “7018” gives you important info about the rod:
- 70 stands for 70,000 psi tensile strength
- 1 means it can be used in all positions—flat, vertical, overhead
- 8 points to a low-hydrogen flux coating with iron powder, suitable for AC or DC+ power
That low-hydrogen coating isn’t just a bonus—it’s essential for preventing weld cracking, especially on high-carbon steel or thicker metal. That’s why 7018 is widely used in structural fabrication, pressure vessels, and heavy-duty repair work.
Arc Feel and Weld Quality
7018 has a reputation for running smooth with minimal spatter. The arc is soft and steady, making it easier to control once you get the feel for it. Many welders say it lays down a bead that looks almost like it’s been TIG welded—tight ripples, easy slag removal, and good tie-in.
If you’re running a pass on thick plate or welding uphill in your shop, this rod can help deliver consistent results. Just don’t rush it. The puddle freezes a little slower than other rods, so controlling your travel speed is key.
Plenty of hobby welders and pros alike say switching to 7018 helped them improve their bead appearance and overall technique.
Machine Setup and Compatibility
One of the great things about 7018 is its flexibility. It works with both AC and DC+ machines, which makes it a solid option for everything from basic buzz boxes to modern inverter welders.
That said, not all AC machines deliver the same arc quality. If you’re using an older transformer model, a 7018AC rod is worth considering—it’s designed for smoother starts on low-voltage equipment.
Moisture is a bigger deal with this rod than others. If it absorbs too much humidity, hydrogen can creep into your welds and lead to cracks. For home use, an airtight container with silica packs usually does the trick. But if you’re working under code or on pressure-rated jobs, proper rod ovens and reconditioning are a must.
Learning Curve and Safety Factors
7018 has a little learning curve compared to easier rods like 6013. It takes a steadier hand and more attention to puddle control. But once you figure it out, you’ll find it opens the door to more serious welding jobs.
It’s also a solid choice for practicing out-of-position welding. The slag peels off clean, and the rod gives you the kind of feedback that helps improve your timing and heat control.
One thing to keep in mind: it produces more fumes than lighter rods due to the iron powder in the coating. So if you’re welding in a garage or enclosed space, good ventilation or a respirator is a smart idea.
Conclusion
7018 rods are all about strength, control, and versatility. They take a little more skill and care, but they’re a great tool to have once you’ve got the hang of them.
Why it stands out:
- Strong welds (70,000 psi)
- All-position capability
- Runs on both AC and DC
- Minimal spatter with clean slag removal
What to watch out for:
- Must be kept dry to avoid hydrogen issues
- Slightly more advanced for beginners
- Heavier fume output—ventilation helps
If you’re planning to tackle structural work, learn vertical welding, or just want to upgrade your skills, mastering 7018 is a smart step forward.