Discover What Stick Welding Is Used For Across Trades and Projects
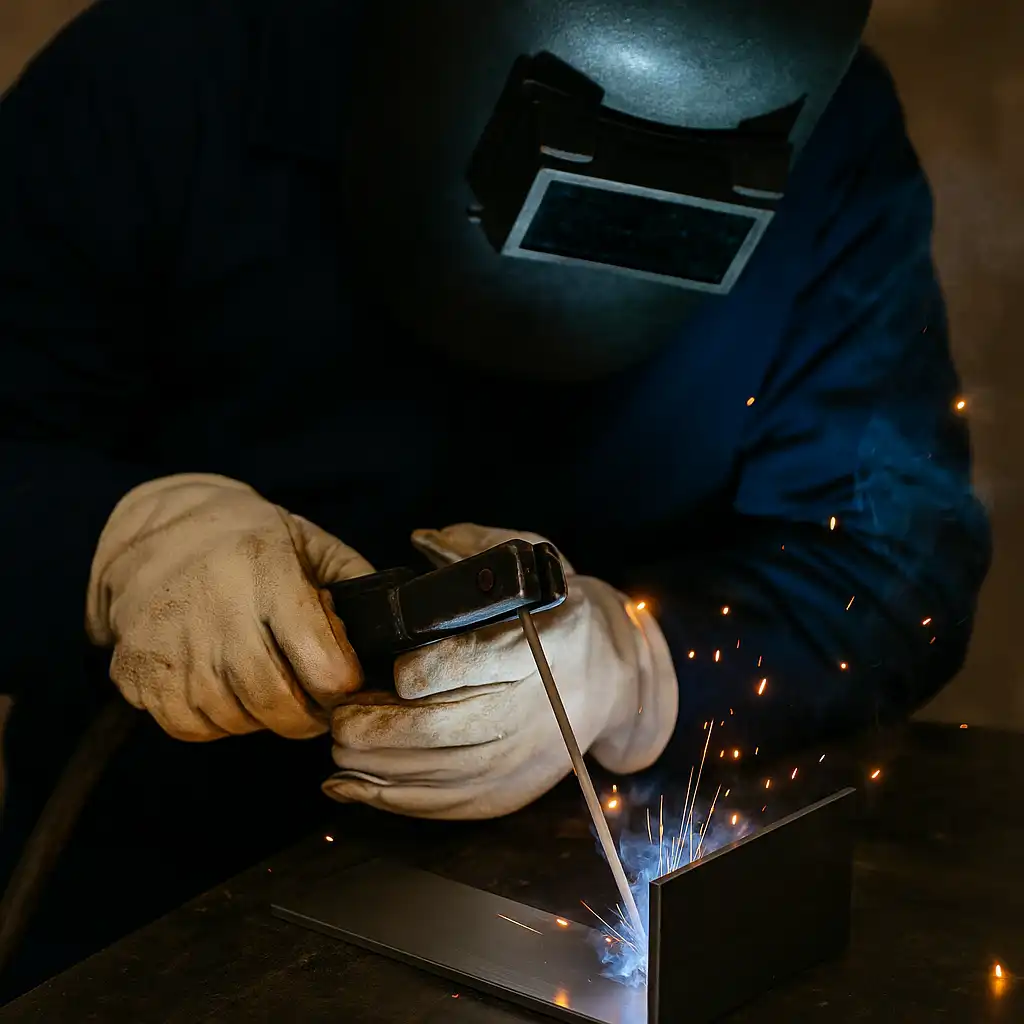
Disclosure: This post contains affiliate links. As an Amazon Associate, I earn from qualifying purchases—at no extra cost to you.
Stick welding remains a trusted method for joining metal in demanding environments, offering a rugged, reliable solution when other processes fall short. Also known as shielded metal arc welding (SMAW), it stands out for its simplicity, portability, and adaptability. While it may not always produce the cleanest welds, its ability to work in tough conditions makes it indispensable in multiple industries. Whether you’re building a fence or maintaining a pipeline, stick welding is often the technique that gets the job done.
Understanding Stick Welding
Stick welding uses a consumable electrode coated in flux to create the weld. An electric current flows through the stick, forming an arc between the electrode and the base metal. The intense heat melts both the electrode and the metal surface, fusing them together. As the flux coating burns off, it produces a protective gas and slag layer that shields the weld from contamination.
Unlike MIG or TIG welding, stick welding does not require external shielding gas, making it an ideal choice for outdoor or windy conditions. This simplicity is one of the reasons it’s so widely used in field applications.
Common Applications in Construction
Stick welding plays a vital role in the construction industry, particularly in structural steelwork. Beams, columns, and joints in buildings often rely on SMAW for its deep penetration and strong bonds. It’s commonly used to fabricate and erect steel frameworks, reinforcing bars, and support structures.
Because it can perform in less-than-ideal conditions, it’s often chosen for on-site welding where wind, moisture, and dirt might otherwise compromise other techniques.
Manufacturing and Heavy Equipment Repair
In manufacturing and repair settings, stick welding is frequently used to maintain heavy machinery. Bulldozers, cranes, trucks, and tractors experience stress that can lead to cracks or joint failures. Stick welding allows operators to patch and reinforce worn parts with precision and durability.
The process is also compatible with a variety of metals, including mild steel, cast iron, and low-alloy steel, making it a go-to for shops that handle diverse repair tasks.
Pipe Welding and Infrastructure
Another major application of stick welding is in pipeline construction and maintenance. Whether laying oil and gas lines or water transport systems, SMAW is relied upon for its strong, consistent welds that can withstand pressure and environmental exposure.
Its ability to create quality welds in various positions—flat, vertical, overhead, or horizontal—makes it especially useful for pipe welders working in the field.
DIY Projects and Farm Equipment
Stick welding isn’t reserved for professionals. Many DIYers and hobbyists prefer it for its cost-effectiveness and ease of use. From repairing a broken gate hinge to constructing a metal trailer, home users find stick welding accessible and effective.
It’s also widely used in rural areas to repair farm equipment. Tractors, plows, fencing, and barns often rely on stick welding for ongoing upkeep.
Conclusion
Stick welding continues to serve as one of the most versatile and dependable welding processes. Its resistance to harsh environments, compatibility with various metals, and relatively low equipment cost make it essential for professionals and DIYers alike. Whether on a construction site, in a repair shop, or on a farm, stick welding is often the backbone of metal joining tasks that require strength and simplicity.