What Is 6G in Welding? Why It’s a Must-Know for Serious Welders
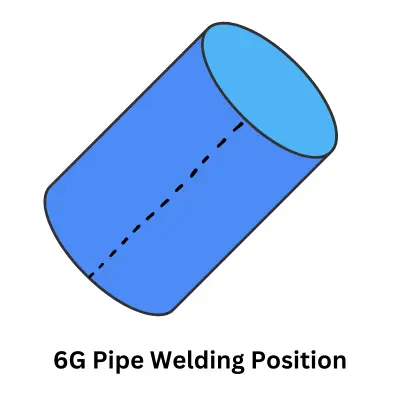
Welding certifications come in many forms, but 6G stands out as a benchmark of skill and precision. It’s not just a technical title—it’s a sign you’re ready for some of the toughest, most in-demand welding jobs out there.
Whether you’re aiming to expand your capabilities or land more competitive positions in the field, understanding what 6G welding really involves can help you decide if it’s worth the effort—and how to start preparing.
What Makes 6G Welding So Challenging?
In 6G welding, you’re working on a pipe that’s fixed at a 45-degree angle. You can’t rotate it. That means you’re welding in nearly every position—flat, horizontal, vertical, and overhead—all in one pass. It’s a true test of technique, consistency, and control.
Many employers use the 6G position as a certification standard because it proves you can handle a wide range of welding angles in high-pressure settings, like pipework or structural installations.
Learning the 6G Position Takes Time
There’s no shortcut here. Getting comfortable with 6G typically involves working your way up through simpler positions like 1G, 2G, and 5G. Feedback from instructors and welding forums suggests that jumping straight into 6G can overwhelm even experienced welders.
Most welders learn it using Stick (SMAW) or TIG, since both demand a steady hand and careful heat control. If you’re just starting out, expect a learning curve—but know that it’s one of the most rewarding certifications you can earn.
Equipment That Makes Practice Easier
If you’re training at home or in a small shop, the right gear can make a big difference. A quality TIG or Stick machine with precise amperage control is a good place to start. A sturdy pipe stand helps keep everything stable during practice.
You’ll also want a reliable auto-darkening helmet—especially one with a large viewing area to reduce neck strain. Some welders recommend using flexible torches or extension handles to navigate tight spaces more comfortably while welding at odd angles.
Safety Needs to Stay Front and Center
Welding at different angles comes with unique risks. Since your body positioning changes throughout the weld, you’ll often be working over, under, and around the pipe. That means slips, burns, and poor visibility are real concerns.
Always wear flame-resistant gear, long gloves, and a well-fitted helmet. If you’re welding indoors or in tight spaces, make sure you have plenty of ventilation or a fume extractor. Good lighting also helps, especially when you’re working around the far side of a pipe.
Conclusion
6G welding is one of the toughest positions to master—but once you do, it opens up serious career opportunities. It’s a skill that shows dedication, control, and versatility. If you’re planning to work in pipe welding, shipbuilding, or heavy construction, this certification is a powerful asset.
Take your time, build up your technique, and invest in the right gear to make your training smoother. It’s not an easy road—but for many welders, it’s one of the most worthwhile steps they’ve taken.