Welding Terms and Definitions That Actually Matter in the Shop
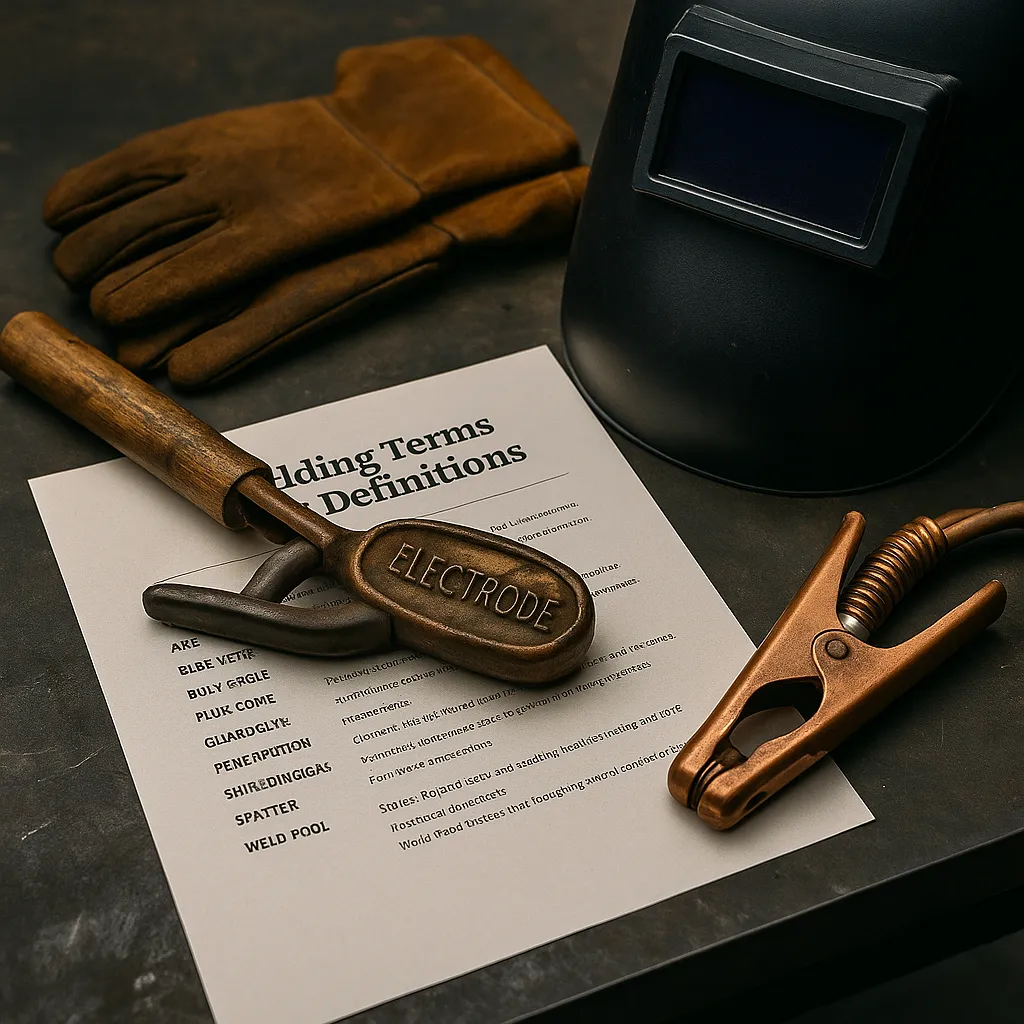
Disclosure: This post contains affiliate links. As an Amazon Associate, I earn from qualifying purchases—at no extra cost to you.
Welding comes with its own language—and if you don’t speak it, things can get confusing fast. Whether you’re flipping through a welder manual or talking to someone in the shop, these terms pop up everywhere. Understanding what they mean will make your learning curve smoother, your welds better, and your gear choices smarter.
Let’s break down the terms and definitions that you’ll actually use, with context to help them stick.
Welding Process Terms That Set the Stage
Each welding process serves a specific purpose. Knowing the difference helps you match the tool to the task.
MIG Welding (Metal Inert Gas)
This beginner-friendly process uses a wire feed system and shielding gas. It’s great for auto repairs, DIY builds, and light fabrication. The ease of use and speed make MIG a popular choice in home garages.
TIG Welding (Tungsten Inert Gas)
TIG delivers clean, precise welds. It’s the go-to for stainless steel, thin metals, or anything that needs a clean finish. It takes more time to learn but gives unmatched control for detailed work.
Stick Welding (Shielded Metal Arc Welding)
Rugged and reliable, stick welding doesn’t need gas. It works well outdoors, on dirty or rusty metal, and in tight corners where portability matters.
Flux-Core Welding (FCAW)
This is a MIG alternative that uses wire with built-in flux, making it ideal for outdoor work and thick steel. It doesn’t need shielding gas, which adds convenience for field jobs.
Practical Shop Vocabulary
These are the words you’ll hear tossed around constantly in any welding space.
Electrode
The piece that conducts electricity to form the arc. It can be a stick, wire, or tungsten rod depending on the process you’re using.
Weld Pool
The molten puddle created during welding. You’ll guide this to control the shape and depth of your bead.
Shielding Gas
Used in MIG and TIG welding, it protects the weld from oxygen and other contaminants. Without it, you’ll get porosity and weak bonds.
Ground Clamp
Connects your workpiece to the welding machine to complete the circuit. Without it, you won’t get an arc.
Terms That Affect Weld Quality
When you start tuning settings or evaluating your welds, these are the concepts to watch for.
Arc Stability
A steady arc makes for smoother, cleaner welds. MIG and TIG tend to offer better stability, especially for new welders.
Duty Cycle
This tells you how long your welder can run before it needs to cool down. A 30% duty cycle at 150 amps means 3 minutes of welding for every 10.
Penetration
How deep the weld fuses into the base metal. More penetration usually means stronger welds. Too little? You risk a weak joint.
Spatter
Small bits of hot metal that fly off during welding. Excessive spatter can be caused by poor settings or technique and leads to more cleanup.
Safety and Equipment-Specific Terms
Some terms are all about protecting yourself and getting the job done right with the right gear.
Auto-Darkening Filter (ADF)
Modern welding helmets use ADFs to protect your eyes the moment you strike an arc. They’re a must for comfort and eye safety.
Respiratory Protection
Some welding fumes are hazardous, especially when working indoors or with galvanized steel. A good respirator or PAPR system can protect your lungs.
Amperage and Voltage
Amperage controls heat. Voltage affects arc length. Understanding both helps you avoid burn-through or cold welds.
Base Metal and Filler Metal
The base metal is what you’re welding. The filler is the material added during the process. Make sure they match or you risk weld failure.
Conclusion
Learning welding terms doesn’t have to feel like studying for an exam. When you break them down with real shop context, they’re actually pretty intuitive. As your skills grow, this vocabulary becomes second nature—and that gives you a huge edge whether you’re adjusting settings, troubleshooting, or just trying to sound like you know your stuff.