The Future of Welding Technology: What’s Changing and Why It Matters
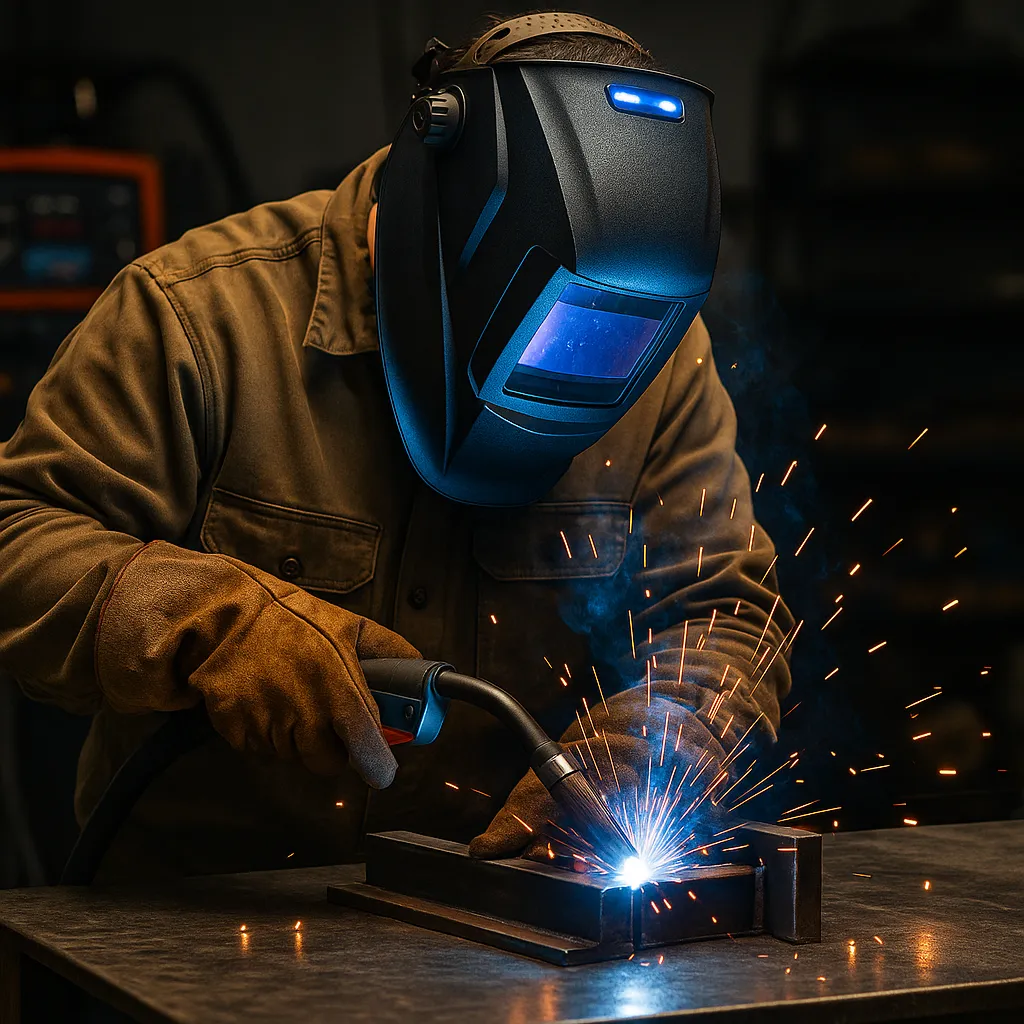
Disclosure: This post contains affiliate links. As an Amazon Associate, I earn from qualifying purchases—at no extra cost to you.
Welding is going through a major shift. New tools and smarter machines are changing how welders work—whether it’s in a home garage or a full-scale fabrication shop. And these changes aren’t just hype. From easier setup to better safety gear, the future of welding looks more efficient, more precise, and a whole lot more user-friendly.
Let’s break down where welding technology is headed and how these updates are already making an impact for both beginners and experienced pros.
Smarter Machines That Simplify Setup
Modern welders aren’t just metal boxes with knobs anymore. They’re packed with tech that makes them easier to use—even if you’re new to the trade. Many models now include digital displays, memory settings, and automatic setup features that adjust wire speed and voltage for you.
Welders on forums and YouTube often highlight how these auto-settings help cut down on trial and error. If you’re switching from welding mild steel to aluminum in the same afternoon, machines with pre-programmed modes make that transition a lot smoother.
Improved Arc Stability for Better Welds
Arc performance can make or break your work—and today’s welders are much more stable and precise than the machines from just a few years ago. Leading brands like Lincoln and Miller are integrating advanced waveform controls into more accessible models.
This means you get smoother starts, less spatter, and cleaner beads—even when working on tricky materials like stainless or thin aluminum. Based on community feedback and product specs, pulse MIG and AC TIG features are no longer limited to top-tier equipment. They’re showing up in mid-range machines, giving weekend welders access to pro-level arc control.
Safety Gear That Works Smarter, Not Harder
Welding safety is also getting an upgrade. Helmets now react faster, provide better clarity, and even adjust the lens shade based on the arc brightness. Some models offer panoramic views and built-in respirators—perfect for long sessions in tight, poorly ventilated areas.
And it’s not just the helmets. Machines are coming with built-in protections like thermal shutdown, anti-stick functions, and fan-on-demand cooling systems. These features help reduce downtime and create a safer, more comfortable working environment.
Automation That Fits Small Shops
Automation isn’t just for factory floors anymore. Small fabrication shops and even solo welders are beginning to explore semi-automated tools like CNC plasma cutters and programmable welding positioners.
While full robotic welders might still be out of reach for most, many users report real efficiency gains from basic automation—especially when building repeat parts or fixtures. AI-assisted welders are still emerging, but they’re a clear sign that hands-on welding and machine learning are beginning to overlap in practical ways.
Conclusion
Welding technology is moving fast—and it’s opening doors for more people to get involved, work safer, and create better results with less hassle.
What’s improving:
- Easier setup with smart controls and digital presets
- Better arc quality, even on difficult materials
- Safer, more comfortable gear for long sessions
- Growing automation tools for faster, cleaner work
What to keep in mind:
- Newer machines can be pricey
- Some tech features take time to learn
- Small shops may need to adapt to automation tools
If you’re just starting out, go for a machine with helpful presets and solid safety features. If you’re running a side hustle or small shop, investing in upgraded gear could save you time—and headaches—down the road.