How to Select a Welder for Farm Use Without Guesswork
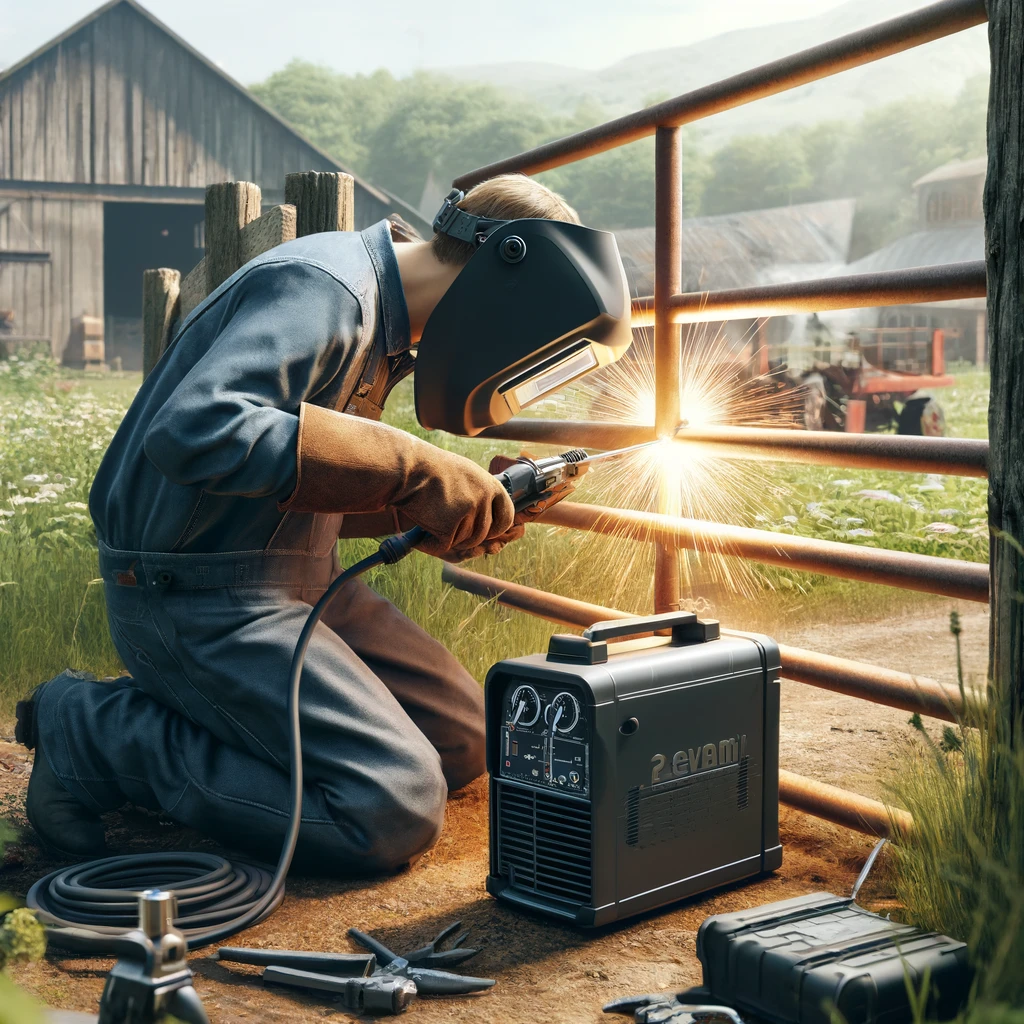
On a farm, things break—gates, implements, trailers, fences—you name it. And when they do, you don’t have time to haul equipment into town or wait days for a repair crew. That’s why every farm should have a reliable welder. But picking the right one isn’t just about grabbing what’s on sale at the local hardware store. It’s about getting a machine tough enough for outdoor elements, versatile enough for odd jobs, and simple enough to run without a welding degree. So how do you choose the right welder for farm use? Let’s dig in.
Consider What You’ll Be Welding
Before buying a welder, take stock of the kinds of repairs and fabrications you’ll actually be doing. Are you fixing rusted gates? Reinforcing tractor attachments? Repairing trailers or livestock pens? These jobs often involve mild steel and thicker materials—usually in the 1/8 to 1/4 inch range. That means you’ll need a welder with enough amperage and power to penetrate heavy metal without overheating.
Stick welders (SMAW) are ideal for these types of jobs because they can handle dirty, rusty metal and don’t need shielding gas—perfect for fieldwork. But if you’re also planning on welding thinner materials or want cleaner, prettier welds, a multi-process welder with MIG capabilities might be worth the upgrade.
Choose the Right Power Supply
Most farms have access to 240V power in the workshop or barn but not always out in the field. That’s where portability becomes crucial. Some welders run on 120V for flexibility, but keep in mind that they’re generally limited in thickness capacity. Dual-voltage machines offer the best of both worlds: plug into 240V for heavy-duty shop work or use 120V for quick jobs closer to the house.
If you’ll be doing remote repairs, consider a welder-generator combo. These rugged units combine power and welding functionality—especially handy when there’s no outlet for miles.
Portability and Durability Matter
Let’s be honest—farm life is tough on gear. Your welder will likely live in a barn, back of a truck, or under a bench layered in dust. Look for a machine built to take abuse. Metal casing, weather-resistant components, and reliable thermal protection systems will keep it running longer.
Weight matters too. You don’t want to haul a 90-pound machine into the pasture for a fence fix. If mobility is key, look for a compact inverter welder. They’re lighter, more efficient, and often pack just as much punch as their heavier transformer cousins.
Ease of Use for Quick Fixes
A welder that’s overly complicated is going to sit in the corner, gathering cobwebs. You want something that’s intuitive—simple knobs, clear displays, and quick setup. Stick welding is generally the easiest to learn and maintain. But if you’re working in the shop with clean metal, MIG is fast and user-friendly too.
Multi-process welders (Stick, MIG, TIG) offer flexibility if you’re open to learning, but if you want to get in and out fast, a solid stick welder may be all you need.
Conclusion: Rugged, Reliable, Ready to Work
Choosing a welder for farm use isn’t about getting the biggest, baddest machine out there—it’s about getting one that fits your work style, environment, and repair needs. Go for durability, portability, and enough power to handle your toughest jobs. Whether you’re repairing a gate in the rain or fabricating a hay rack in the barn, the right welder makes all the difference.