How Do I Weld Aluminum with a MIG Welder: Step-by-Step Process
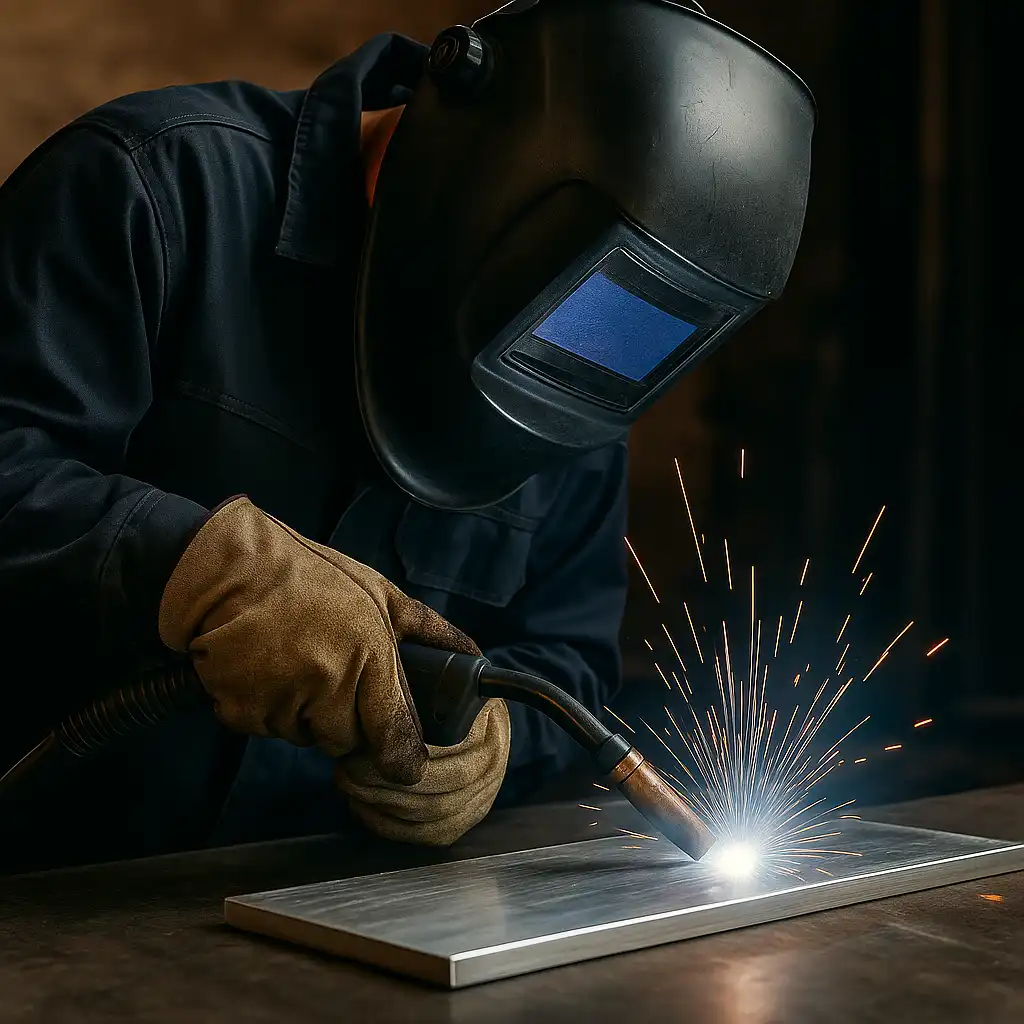
Disclosure: This post contains affiliate links. As an Amazon Associate, I earn from qualifying purchases—at no extra cost to you.
Welding aluminum with a MIG welder can be intimidating for beginners, but with the right setup and technique, it’s absolutely achievable—even at home. While aluminum’s properties differ from steel, a few adjustments in equipment and approach will help you achieve strong, clean welds without frustration.
Understanding Aluminum’s Welding Challenges
Aluminum is a soft, lightweight metal with high thermal conductivity and an oxide layer that melts at a much higher temperature than the metal itself. This makes it more sensitive to heat and harder to weld than steel, especially when using MIG. However, once you grasp the fundamentals, it becomes much easier to manage.
Choose the Right MIG Welder and Wire
To weld aluminum, you’ll need a MIG welder capable of running spool guns. A spool gun feeds soft aluminum wire more reliably than a standard torch setup. Look for a machine that allows adjustments in voltage and wire feed speed for better control.
Use 100% argon shielding gas and aluminum wire such as ER4045 or ER5356. Choose the wire diameter based on the thickness of the metal—typically 0.030 or 0.035 inches.
Prepare the Work Surface Properly
Cleanliness is critical when welding aluminum. Use a stainless-steel brush or acetone to remove any oxidation and surface contamination. Do not use the same brush used for steel, as contamination can lead to poor weld quality. Also, make sure your base metal is clamped securely and has proper contact for grounding.
Set the Correct Welding Parameters
Set your MIG welder to the appropriate voltage and wire feed speed for aluminum. These settings vary based on the thickness of the material and the wire diameter, so consult your welder’s manual for specific ranges.
Aluminum typically requires higher voltage than steel, and a wire feed that is too slow can lead to burn-through. Begin with a short arc, and always do a few practice passes on scrap aluminum before working on the actual piece.
Master the Push Technique
Unlike steel, aluminum should always be welded using the push method. Angle the MIG gun 10–15 degrees away from the weld and push the puddle forward. Pulling can result in contamination and poor penetration.
Be ready to move quickly, as aluminum heats up fast and can warp if you dwell in one area too long. Keep a steady hand and maintain a consistent travel speed to create even, shiny weld beads.
Common Mistakes to Avoid
- Using mixed gases like C25 (75% Argon / 25% CO₂) meant for steel.
- Not cleaning the aluminum thoroughly before welding.
- Attempting to use a standard MIG torch without a spool gun.
- Using a pull technique instead of pushing.
By avoiding these errors, you’ll set yourself up for smoother welds and stronger results.
Conclusion
Learning how to weld aluminum with a MIG welder involves adapting your tools and techniques to the unique properties of this metal. With a spool gun, pure argon gas, and proper surface prep, even a hobbyist can produce clean and durable aluminum welds at home. Practice on scrap pieces, refine your settings, and always prioritize safety as you build your skills.