Aluminum 6061 T6 vs T651: Key Differences for Welding and Machining
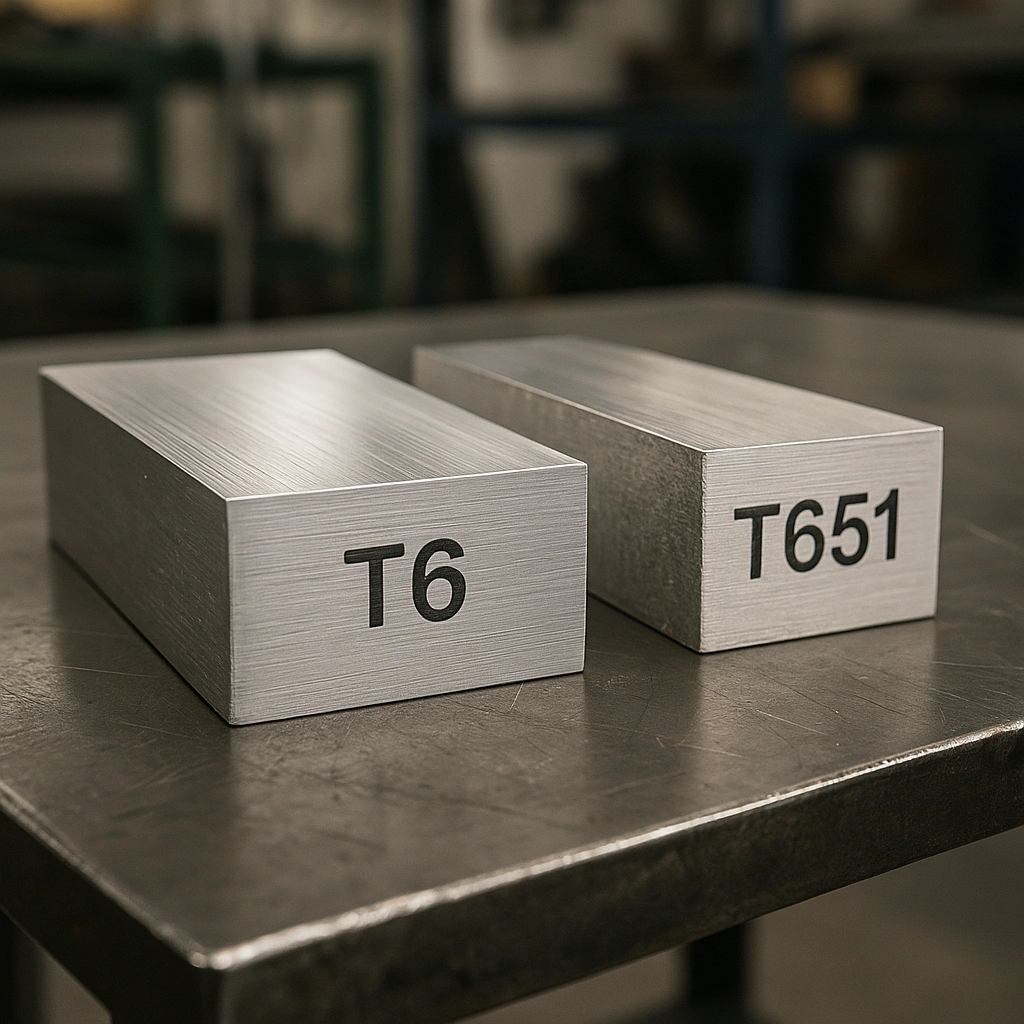
Disclosure: This post contains affiliate links. As an Amazon Associate, I earn from qualifying purchases—at no extra cost to you.
When you’re working with aluminum, 6061 often ends up being the go-to choice. It’s strong, versatile, easy to weld, and machines well. But once you start ordering material, you’ll likely see two common options: 6061 T6 and 6061 T651.
At first glance, they seem almost identical. However, there are important differences that can affect your project, especially if you’re machining precise parts, welding frames, or building something where flatness matters.
Let’s break it down so you can confidently pick the right one for your job.
How T6 and T651 Are Processed
Both T6 and T651 start as 6061 aluminum alloy. They go through heat treatment and artificial aging to reach full strength. At this stage, 6061 T6 is ready for use. T651, however, goes through one extra step — it’s stretched slightly after heat treating to relieve internal stress.
According to manufacturer data and supplier info, this stress relief helps prevent warping during machining or welding. Many small shop machinists notice that T651 tends to stay flatter and more stable, especially when working on larger parts or precision projects that require tight tolerances.
Stability During Machining
CNC operators and job shop welders often mention that T651 is more stable once machining begins. Because of the stress-relieving process, it doesn’t shift or move as much when you’re removing material.
When machining flat plates, brackets, or components like engine mounts or robotics parts, T651 helps avoid warping after multiple passes.
That said, T6 still performs well for smaller parts or projects where you’re not chasing extreme precision. Many hobby welders and fabricators report no major issues when using T6 for everyday shop work.
Welding Performance
For welding, both T6 and T651 behave the same. Underneath, they’re still 6061 aluminum. The main challenge with either is preventing post-weld cracking in the heat-affected zone.
Welder feedback from forums suggests preheating thicker sections to around 300°F and using filler rods like 4045 or 5356 to help reduce cracks. Since welding weakens both tempers in the joint area, neither has a major edge here.
Garage welders often say they’ve successfully welded both versions, as long as they control heat input and prep their joints properly. For typical fabrication work — like frames, tool carts, or trailer repairs — either one will handle the job.
Price, Availability, and Everyday Use
You’ll usually find T651 priced slightly higher than T6 due to the extra processing involved. For most small projects, though, the price difference isn’t dramatic.
According to suppliers, T651 is more common in flat plates, while T6 shows up more often in extrusions like tubing, angle, or channel. Sometimes, what you use simply comes down to which form you need.
For general welding and fabrication work — such as gates, frames, or shop projects — most fabricators stick with 6061 T6. It’s widely available and easy to work with. When machining parts that need to stay perfectly flat or cutting large plates, many shops say T651 is worth the upgrade.
Conclusion
Both 6061 T6 and T651 are excellent choices for welding, machining, and general fabrication. The big difference is stress relief. T651’s added processing helps maintain dimensional stability, making it better for machining or large flat parts.
If you’re welding or fabricating general projects, 6061 T6 will handle most tasks with no problem. But if you’re machining precision parts or working on thick plates that need to stay flat, T651 can help you avoid costly warping and rework.
Related Articles You Might Find Helpful
Here are a few more posts that can help with your aluminum welding and fabrication work: