Can You TIG Weld Without Gas? Why Shielding Gas Is Non-Negotiable
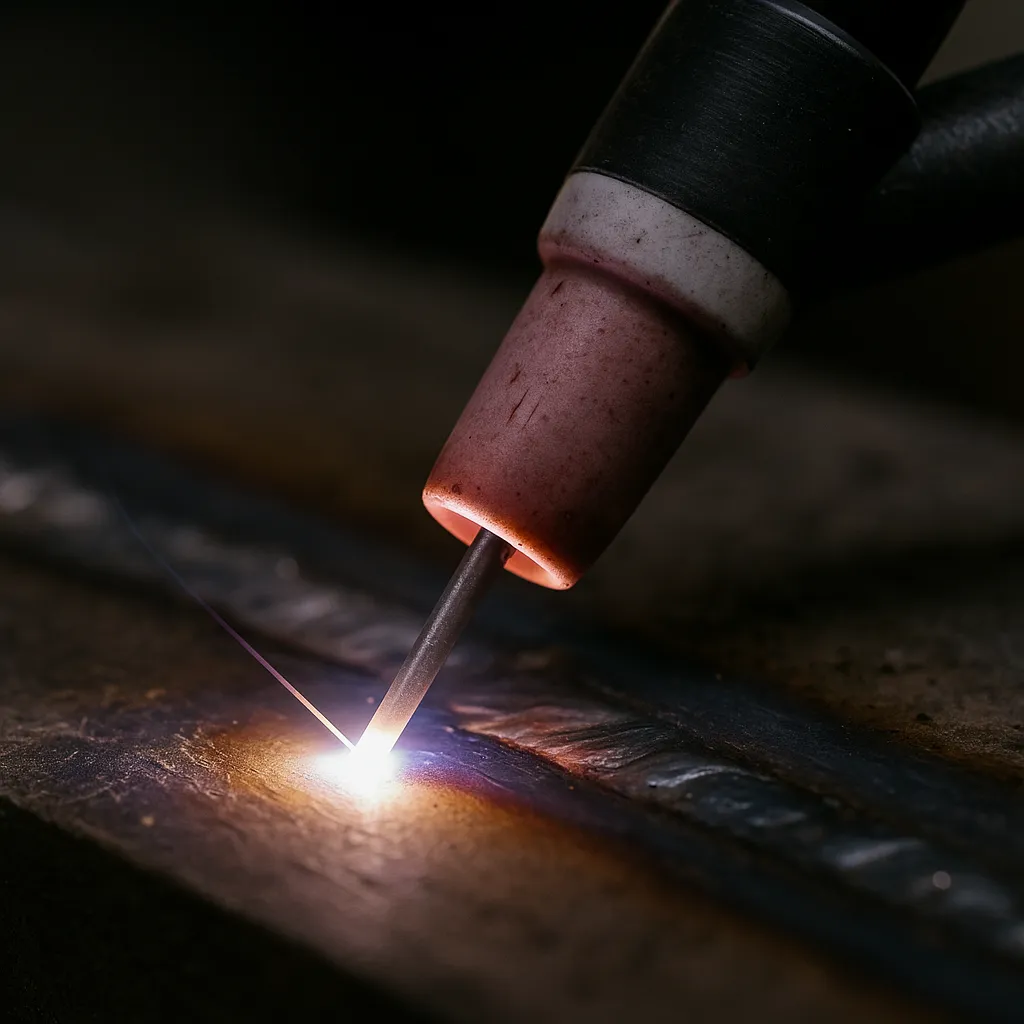
Disclosure: This post contains affiliate links. As an Amazon Associate, I earn from qualifying purchases—at no extra cost to you.
TIG welding depends on shielding gas to protect your weld from contamination. Unlike processes like stick or flux-core MIG, TIG doesn’t have built-in flux to keep oxygen and moisture out. Without gas, things start to go wrong almost immediately.
Still, many beginners wonder if they can skip the gas to save a little money or get by with limited gear. Here’s a clear look at what happens when you attempt TIG welding without gas, based on welder feedback, real-world shop experience, and community reports.
The Arc Becomes Unstable Almost Immediately
Once the gas is gone, arc stability quickly breaks down. According to welders who’ve tried it, the arc starts wandering and sputtering within seconds. Instead of a smooth, controlled arc, you get constant flickering and instability.
Many hobby welders say they couldn’t get more than an inch of weld before things started to fall apart. The tungsten oxidizes fast, contaminating the puddle and spitting particles into the weld. Even highly skilled welders struggle to maintain any usable arc without shielding gas.
Contamination Shows Up Right Away
Without gas, oxygen, nitrogen, and moisture attack the molten metal as soon as the arc starts. Welders who’ve experimented with gasless TIG welding report black, grainy, porous welds almost instantly.
You’ll see craters, small holes, and surface frost appear right in the weld pool. The porosity often goes deep, leading to cracks or total failure under even light stress. The tungsten doesn’t hold up well either—it begins degrading within seconds, feeding more contamination into the puddle.
TIG Equipment Simply Isn’t Built for Gasless Welding
TIG machines are designed from the ground up to work with gas. Unlike MIG welders, which offer flux-core wire options, TIG doesn’t have a widely available flux-core alternative.
Some hobbyists have experimented with flux-coated filler rods or other workarounds, but according to most welding forums and user videos, these methods produce poor results. The welds remain weak, messy, and unreliable. Manufacturers strongly advise against running TIG machines without gas.
Safety Risks Increase
Trying to TIG weld without gas doesn’t just result in ugly welds—it can also create serious safety hazards. Welds that appear solid may fail suddenly under load, especially in projects like trailers, railings, or light frames.
Welders often report more arc instability, tungsten spitting, and unpredictable arc jumps, which increase the chance of burns, damaged workpieces, or accidental strikes. These risks are even greater in tight garage spaces or small workshops.
Conclusion
While you can strike an arc with TIG without gas, everything goes downhill right after that. Based on extensive welder feedback and manufacturer recommendations, shielding gas isn’t optional—it’s absolutely essential for clean, strong, and safe TIG welds.
If you’re learning TIG or planning serious projects, invest in the proper gas setup from the beginning. You’ll avoid major headaches and get solid, reliable welds that won’t fail when you need them most.