Can You MIG Weld Cast Iron to Mild Steel Without Cracking?
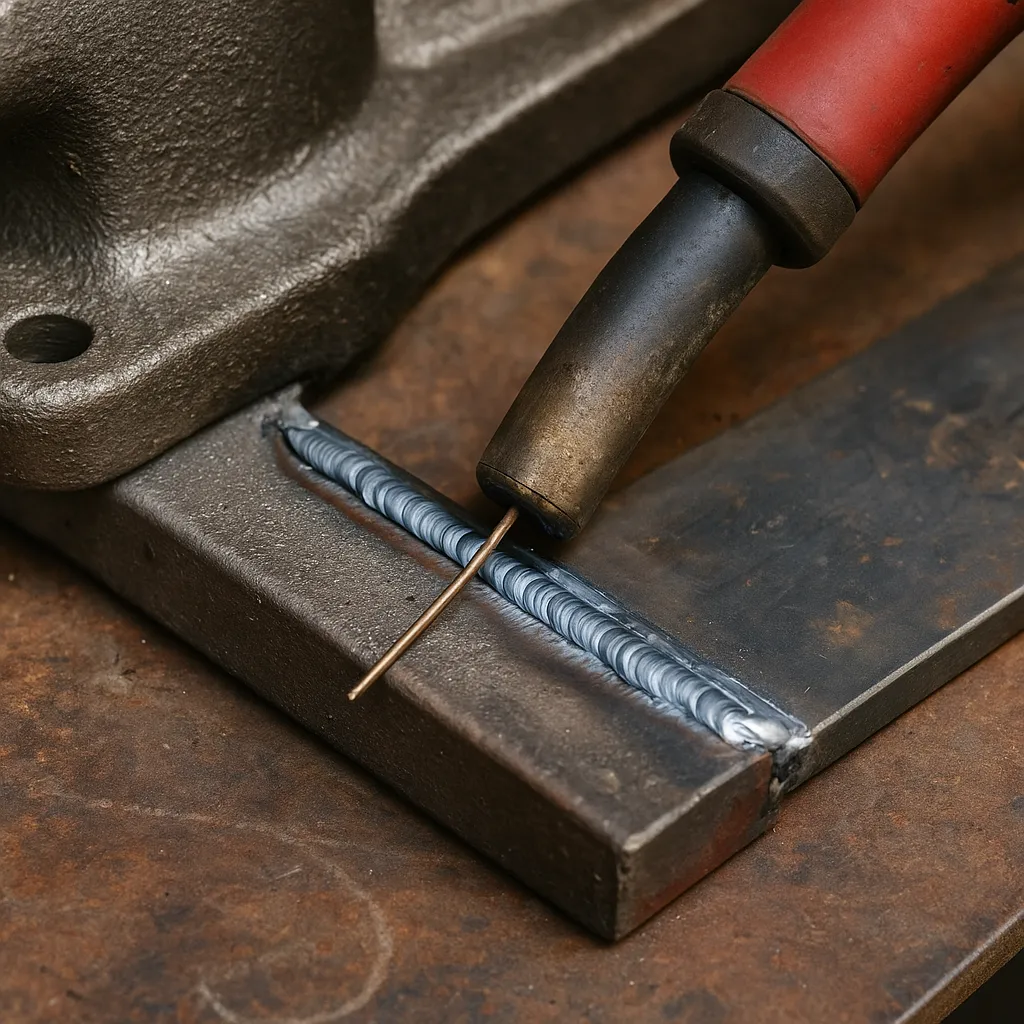
Disclosure: This post contains affiliate links. As an Amazon Associate, I earn from qualifying purchases—at no extra cost to you.
Welding cast iron to mild steel isn’t impossible—but it definitely comes with challenges. The two metals behave very differently under heat. Cast iron is brittle and rich in carbon, while mild steel is more ductile and forgiving. To get a solid weld between them, you’ll need the right filler wire, careful prep, and heat control.
Let’s break down what actually works when you’re trying to join these two materials using a MIG welder.
Cast Iron vs Mild Steel: A Tough Match
The main reason this weld is tricky is that cast iron is high in carbon and doesn’t like quick temperature swings. It’s strong under compression, but brittle when stressed or heated unevenly. Mild steel, on the other hand, welds easily and flexes more under pressure.
Many experienced welders recommend using nickel-based MIG wire, like ERNiFe-CI, when joining cast iron to steel. It’s not cheap, but it creates a more ductile weld and helps prevent cracking. Some hobbyists also try stainless wire like 309L or even ER70S-6 mild steel wire for temporary fixes, but these options aren’t ideal for anything structural or load-bearing.
Why Preheat and Post-Weld Cooling Matter
If there’s one step you don’t want to skip, it’s preheating. Cast iron responds poorly to sudden heat, which is why preheating the cast section to 400°F–600°F can make a big difference. Without it, your weld might crack either during the process or shortly after it cools.
Once you’ve finished welding, let the part cool down slowly. That means wrapping it in a welding blanket or burying it in sand to reduce thermal shock. You’ll also want to avoid running long beads—short stitch welds spaced out over time help control heat input and keep stress to a minimum.
MIG Setup and Filler Wire Options
You don’t need a top-of-the-line welder, but some setups are better suited than others. MIG welders that can run 100% argon or an argon-helium mix tend to deliver better results when used with nickel-based wire. That combo helps reduce cracking and promotes a more stable arc.
If you’re welding something that won’t face a lot of stress, like a tool bracket or fence part, some users report success with more affordable filler wires like 309L or even ER70S-6. Just be aware—these are best for light-duty repairs and not long-term strength.
Real-World Learning Curve
MIG welding cast iron to steel isn’t beginner-level work, but you don’t need decades of experience to pull it off either. Many small shop welders have done it successfully with careful prep and the right filler. According to welding forums and pro insights, success comes down to heat management, proper wire selection, and knowing when to walk away from a poor setup.
If you’re just patching up a cast iron bench leg in your garage, you might get by with mild steel wire and a slow, controlled weld. But for anything critical, investing in the right materials and process is well worth it.
Conclusion
You can MIG weld cast iron to mild steel, but it takes more planning than most welds. Cast iron needs to be preheated and cooled slowly to avoid cracking. Nickel-based wire offers the best performance, especially for critical or high-stress applications. Stainless or mild steel wire might work for light repairs, but they come with trade-offs in strength and durability. If you approach the job with the right prep, wire, and technique, even a basic MIG welder can make this connection work.