Best Welding Technique for Steel: Practical Methods That Actually Work
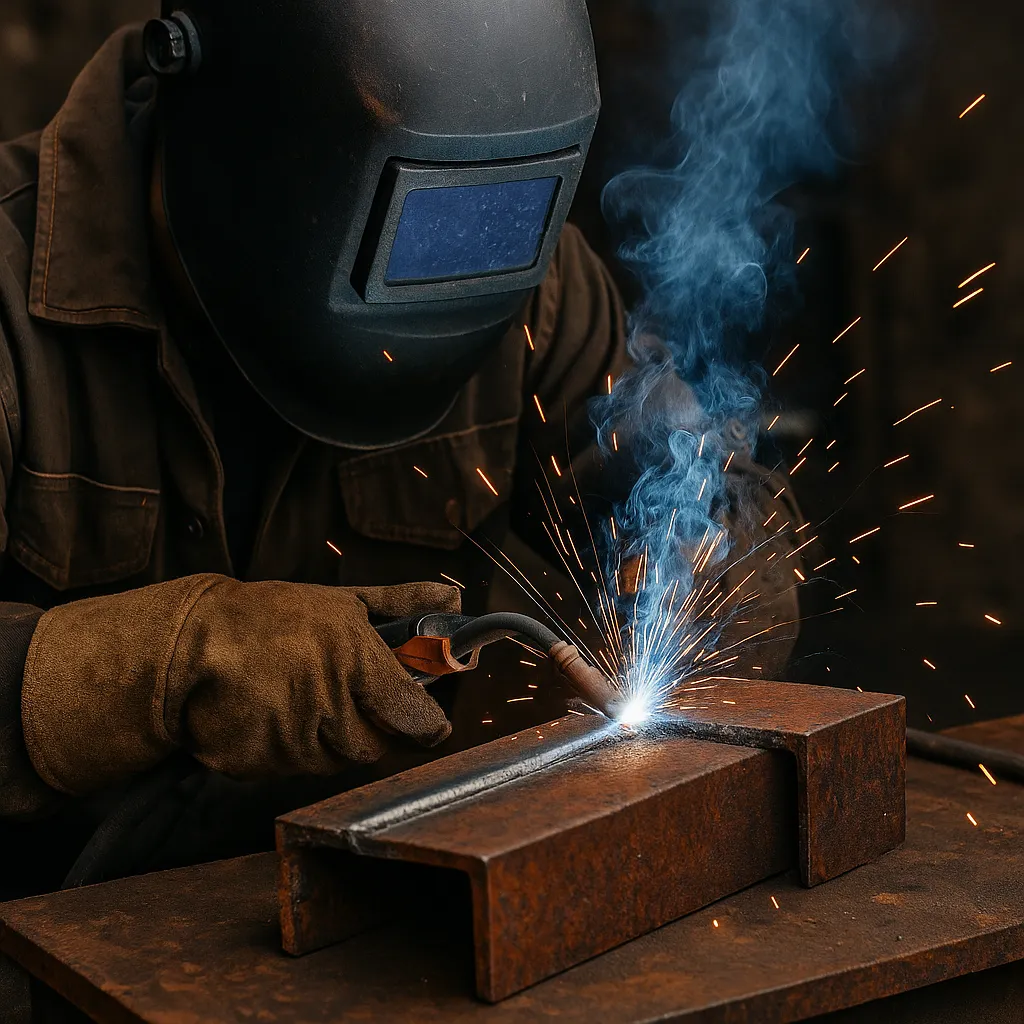
Disclosure: This post contains affiliate links. As an Amazon Associate, I earn from qualifying purchases—at no extra cost to you.
Welding steel is one of the most common tasks welders face, whether it’s for structural repairs, DIY builds, or shop work. Steel is strong, widely available, and adaptable—but picking the right technique makes all the difference in the final result.
Let’s break down the best welding methods for steel and how they stack up in real-world use.
MIG Welding – Fast, Clean, and Great for Mild Steel
MIG welding (Metal Inert Gas) is one of the easiest methods to learn, especially for beginners or those working in home garages. It’s efficient, produces clean welds, and doesn’t require constant rod changes.
It uses a wire-fed spool and shielding gas, making it ideal for thinner sections of mild steel. You’ll see MIG used for auto body work, furniture frames, and home repairs. Since there’s minimal slag, post-weld cleanup is quick.
Many weekend welders prefer MIG because it’s reliable and easy to handle—even without years of experience.
Stick Welding – A Rugged Choice for Dirty or Outdoor Jobs
Stick welding (Shielded Metal Arc Welding) is tougher and more forgiving when you’re dealing with rust, paint, or rough outdoor conditions. It doesn’t rely on external gas, which makes it portable and weather-resistant.
That said, the arc can be harder to control, and there’s more slag to clean. But for structural steel, gates, or machinery repairs in less-than-perfect conditions, it holds strong.
Stick is especially popular on farms, in field repair work, and when access to clean metal is limited.
TIG Welding – Clean, Precise, and Best for Thin Steel
TIG welding (Tungsten Inert Gas) gives you the cleanest, most controlled welds. It’s great for thin sheet metal, stainless steel, and any job where appearance matters.
This method lets you add filler metal separately, so you have full control over the weld. But it’s slower and has a steeper learning curve than MIG or stick.
Welders often turn to TIG when they’re working on roll cages, exhaust systems, or intricate fabrication where quality and looks go hand-in-hand.
Flux-Core Welding – Ideal for Thick Steel and Outdoor Work
Flux-core arc welding (FCAW) is similar to MIG but doesn’t require gas tanks. The wire has flux built in, so it creates its own shielding during the weld. It’s a go-to choice for thick materials and outdoor conditions.
While not as clean as MIG or TIG, flux-core welding penetrates deeper and works well when strength matters more than appearance. Many use it for structural beams, trailer frames, and heavy equipment.
This method is especially handy when welding outside in windy conditions or on dirty metal.
Conclusion
Each steel welding technique brings its own strengths to the table:
MIG is quick and easy for clean mild steel.
Stick offers reliability for tough, dirty, or outdoor work.
TIG delivers precision and beauty on thin or delicate steel.
Flux-core is a powerhouse for thick steel and outdoor projects.
There’s no one-size-fits-all answer. It comes down to what you’re welding, where you’re working, and how polished you want your welds to look. Choose based on the project—and your comfort level—and you’ll be in great shape.