Best Welding for Sheet Metal: Smart Picks for Clean Results
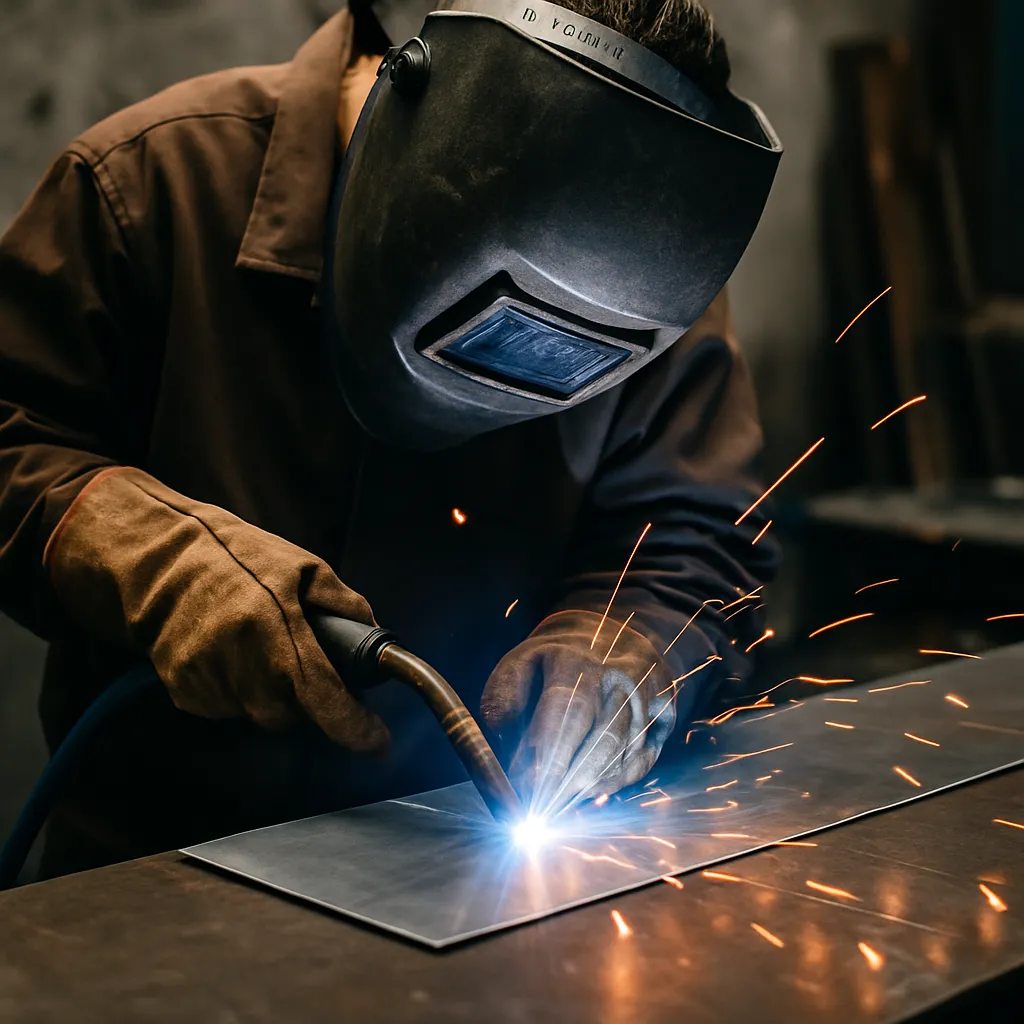
Disclosure: This post contains affiliate links. As an Amazon Associate, I earn from qualifying purchases—at no extra cost to you.
Welding sheet metal is all about control, finesse, and the right method. When you’re working with thin steel or aluminum, choosing the wrong process can lead to warping, burn-through, or messy welds. The good news? There are proven techniques that make the job easier—whether you’re a weekend DIYer or putting together precision parts in your garage shop.
Let’s break down the best welding options for sheet metal and when each one makes the most sense.
MIG Welding: Best All-Around Option for Thin Materials
MIG welding is one of the easiest and most forgiving methods for sheet metal work. It’s especially effective for mild steel in the 18–20 gauge range. Using .023” wire with a 75/25 argon-CO₂ gas mix helps keep the arc smooth and spatter to a minimum. This setup is popular for auto body work and general metal fabrication.
Many newer MIG machines come with synergic settings, letting you dial in voltage and wire speed with minimal guesswork. If you’re just getting started, MIG offers a solid balance of control, affordability, and speed.
TIG Welding: Cleanest Welds, But Steeper Learning Curve
TIG welding gives you beautiful, precise welds—ideal for stainless steel or aluminum sheet. It’s slower and more technical, but you get full control over heat input and filler material. That makes it great for decorative work or when appearance matters.
Most hobbyists use around 60–80 amps and 3/32” tungsten for thin metals. The technique takes time to master, but if you’re willing to learn, TIG is hard to beat for finish quality.
Flux-Core: Not Ideal, but Possible with Care
Flux-core welding is handy when you don’t have access to gas or you’re working outside. However, it’s not the first choice for sheet metal. The process runs hotter than MIG, and that heat can easily cause blowouts or distortion on thinner materials.
Some welders make it work by using short stitch welds and allowing the metal to cool between passes. Still, it’s a more rugged option—expect more spatter and cleanup compared to gas-shielded methods.
Practical Tips for Sheet Metal Welding
Regardless of your welding method, a few setup tricks can help. Using a copper backing plate behind your weld absorbs excess heat and prevents burn-through. It’s a favorite among car restorers and sheet metal fabricators.
Also, use tack welds spaced evenly along the joint before running a bead. This keeps the material aligned and minimizes heat buildup. And don’t forget safety—lightweight gloves and a responsive auto-darkening helmet make a big difference when working with fine details.
Conclusion
MIG welding is usually the go-to for sheet metal—it’s simple, affordable, and versatile enough for most jobs. TIG is your best bet when appearance or precision is key, while flux-core is more of a last resort that can work with the right technique.
Your final choice depends on your tools, experience level, and the kind of work you’re doing. With the right setup, even tricky sheet metal jobs can turn out clean and strong.
Related Articles You Might Find Helpful
- Best MIG Welder for Automotive Sheet Metal: Smooth Welding for Car Panels
- How to Weld Sheet Metal with a Wire Feed Welder: A Beginner-Friendly Guide
- Best Welding for Auto Body
- Does Welding Weaken Metal? What Welders Need to Know About Heat and Strength
- Understanding Metal Fatigue in Welding and How to Prevent It