What Filler Rod for Cast Aluminum to Use for Strong Welds
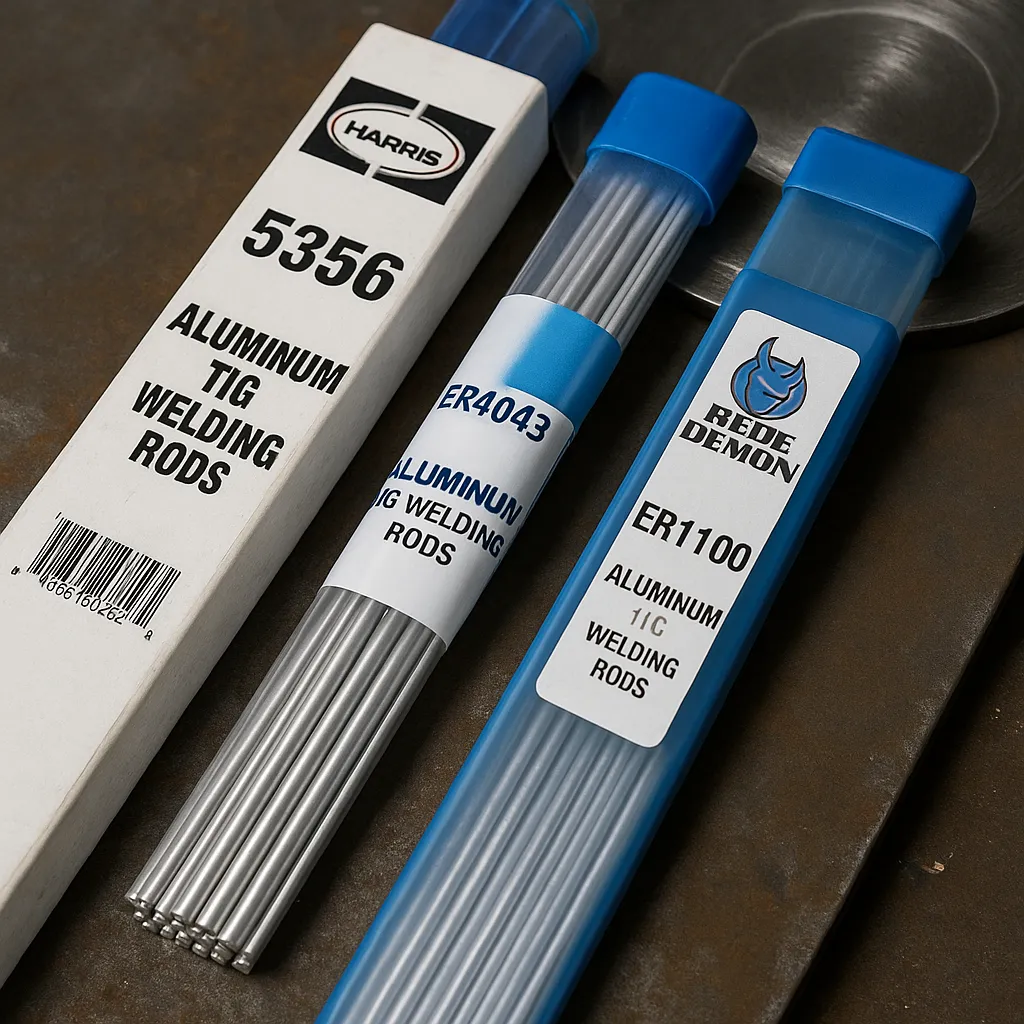
Disclosure: This post contains affiliate links. As an Amazon Associate, I earn from qualifying purchases—at no extra cost to you.
Welding cast aluminum takes more than just the right machine—it starts with the right filler rod. Castings are often old, porous, or full of unknown alloys, and that makes choosing your filler metal a critical step.
Whether you’re patching up a cracked rim or rebuilding a corroded bracket, using the wrong rod can lead to brittle welds, cracking, or frustrating rework. The good news? There are a few time-tested filler rods that welders trust for cast aluminum.
Why Certain Rods Work Better on Cast Aluminum
Not all filler rods handle cast aluminum well. This type of metal can be dirty, inconsistent, and prone to cracking. That’s why rods like ER4043, ER5356, and ER1100 are the usual picks.
ER4043 is the most common choice. It contains more silicon, which helps the weld flow better and reduces cracking. That’s key when working with older or imperfect castings.
ER5356 is a bit stronger. It doesn’t flow quite as smoothly but offers better strength and corrosion resistance—especially helpful in structural or marine applications.
ER1100 is softer and often used for decorative work or repairs on thin, polished aluminum. It won’t handle heavy stress, but it’s great for smooth puddle control and matching appearance.
How Welders Are Using These Rods
If you’re welding something like a cracked alternator housing or cast aluminum mower deck, ER4043 is your best bet. Based on feedback from welding communities and real-world users, it’s easy to control and resists common problems like cracking or porosity.
Welders who work on trailers, boat parts, or outdoor equipment often lean toward ER5356. It handles more stress and holds up better in weathered environments.
For light-duty or cosmetic welds—like custom aluminum enclosures or trim—ER1100 gives you a softer arc and better finish, but it’s not built for structural use.
Setup Tips and Ease of Use
These rods work best with AC TIG welding and a clean surface. Make sure to scrub your part with a stainless steel brush and wipe it down with acetone. Dirty cast aluminum loves to trap contaminants, which leads to pinholes or weak welds.
ER4043 runs smooth and fills gaps nicely without requiring excessive heat. ER5356 can feel a bit hotter, so you’ll need to adjust your amps and travel speed. ER1100 is super forgiving—ideal for new welders or those working with thin material.
All three rods are compatible with most AC TIG machines. If your machine has balance and frequency controls, you’ll be able to fine-tune the arc for even better results.
Check Price & Availability
Here are three popular filler rods that welders trust for cast aluminum jobs:
View on Amazon – WeldingCity ER4043 TIG Rod (1/8″, 2 lb pack)
View on Amazon – Blue Demon ER1100 TIG Rod (3/32″, 1 lb tube)
View on Amazon – HARRIS ER5356 TIG Rod (3/32″, 10 lb box)
Conclusion
When you’re welding cast aluminum, the filler rod you pick can make or break your weld. ER4043 is a great all-around rod for most repair work. It flows well, cracks less, and handles a variety of castings. ER5356 brings extra strength and is better suited for outdoor or high-stress parts. ER1100 is best saved for clean, light-duty applications where appearance matters more than strength.
For DIYers and small shop welders, having both ER4043 and ER5356 on hand covers most needs. Pick the one that fits your project, prep your material properly, and you’ll get solid results.