Vulcan Flux Core Wire Review: Affordable Welding Performance for DIY Projects
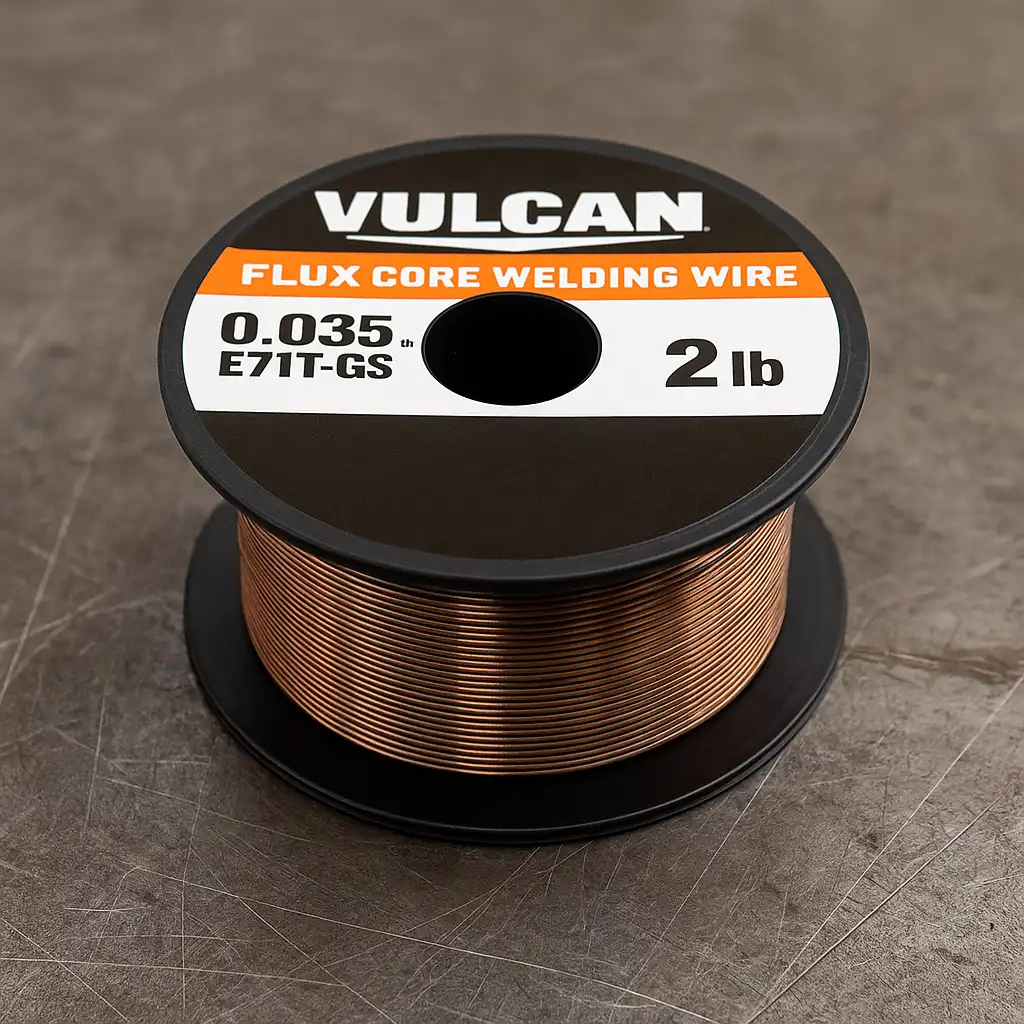
Disclosure: This post contains affiliate links. As an Amazon Associate, I earn from qualifying purchases—at no extra cost to you.
Flux core wire is a go-to option for hobbyists, fabricators, and welders looking to complete solid welds without the need for shielding gas. The Vulcan 0.035 in. E71T-GS Flux Core Welding Wire offers a convenient solution for welding mild steel in outdoor or breezy environments. This 2 lb. spool is designed for self-shielded flux core welding, making it ideal for users of 110V welders or portable machines without gas setups. But does it deliver quality results on a budget? Let’s find out.
Vulcan 0.035 in. E71T-GS Flux Core Welding Wire Review
Vulcan, a Harbor Freight brand, has built a following for providing budget-friendly welding gear with surprisingly solid performance. Their E71T-GS flux core wire is no exception. Sold in a 2 lb. roll and sized at 0.035 inches, it’s compatible with most flux core welders and performs well in home shops and light-duty fabrication jobs.
The E71T-GS designation tells you that it’s a single-pass, self-shielded wire intended for welding galvanized or mild steel without external gas. It’s primarily used for flat and horizontal welds but can be applied vertically with proper technique.
Key Performance Highlights
Smooth Arc and Minimal Spatter
Compared to other low-cost wires, the Vulcan flux core wire offers a relatively smooth arc that is easy to control, even for beginner welders. While flux core always produces more spatter than MIG, this wire leaves less cleanup than expected. Slag is easy to remove with a chipping hammer and wire brush.
Penetration and Weld Strength
The 0.035 in. size provides good penetration on 1/8” to 1/4” steel, making it suitable for common tasks like trailer repairs, brackets, angle iron, and small structural welds. Due to the high heat input, it’s not ideal for very thin sheet metal, but it excels on thicker pieces in a single-pass application.
Ease of Use
This wire feeds well through most hobbyist-grade and light industrial flux core welders. The arc is forgiving, and even first-time users can lay down a decent bead with minimal adjustment. Just be sure to match the correct polarity—DCEN (Direct Current Electrode Negative) is required for flux core welding.
Use Cases and Ideal Projects
This Vulcan flux core wire is best suited for:
- Farm equipment and fence repair
- Automotive patching (on thicker metal)
- Outdoor fabrication where shielding gas isn’t practical
- Small welding projects and maintenance tasks
Because it doesn’t require a gas setup, it’s also great for mobile welding jobs and emergency repairs.
Things to Consider
While the Vulcan flux core wire performs well for the price, it is limited to single-pass welding only and doesn’t hold up as well on multi-pass joints or heavy-duty structural welds. Also, expect moderate fume generation, so proper ventilation or fume extraction is a must.
Conclusion
The Vulcan 0.035 in. E71T-GS flux core wire is a solid choice for budget-conscious welders who want decent results without switching to gas. It’s consistent, beginner-friendly, and ideal for quick repairs and light fabrication. While not designed for heavy-duty or multi-pass work, it more than holds its own in single-pass applications—especially considering the affordable price.