How Does Ultrasonic Welding Work? A Quick Look at This Clean, High-Speed Method
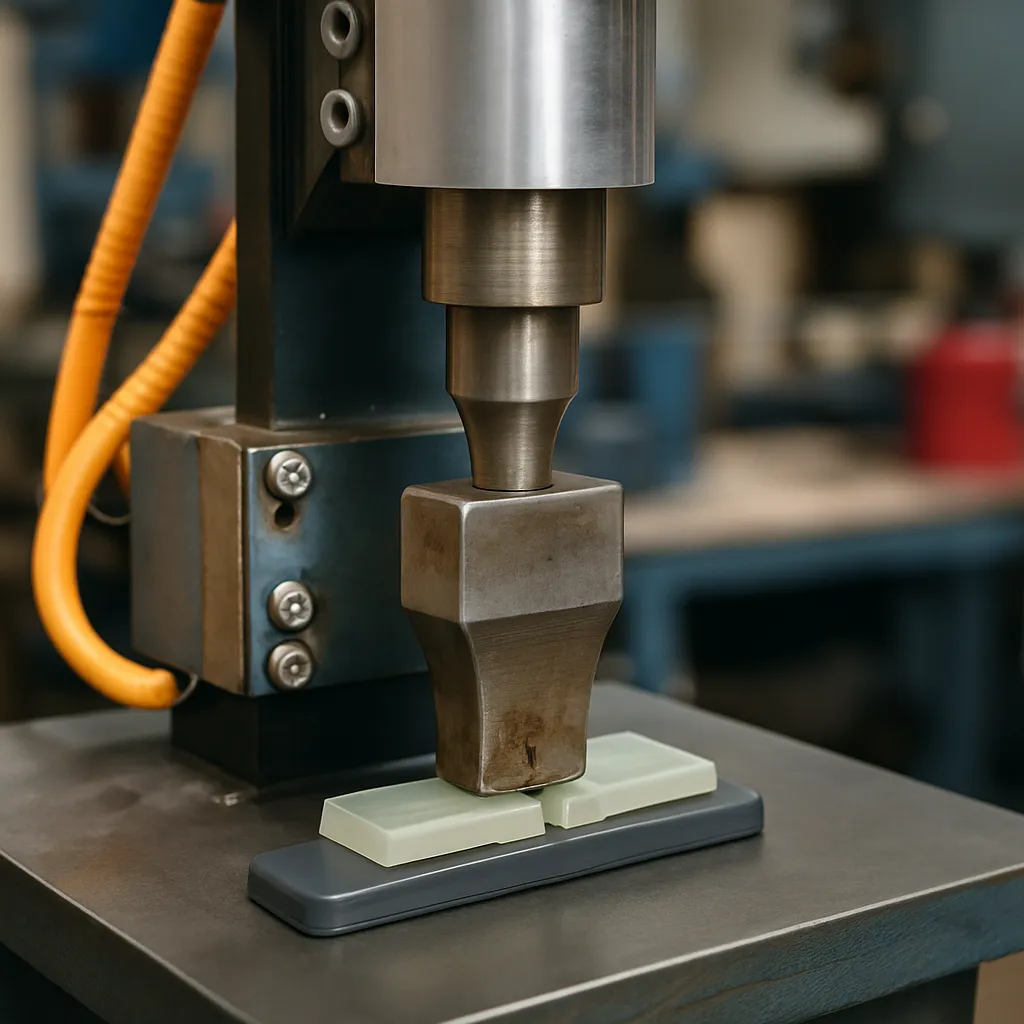
Ultrasonic welding is one of the fastest, cleanest ways to bond materials—especially plastics and thin metals. It skips the open flame, molten puddles, and filler wire. Instead, it uses high-frequency sound waves to create friction and heat between two materials, fusing them in seconds.
This method is widely used in manufacturing for things like electronics, automotive parts, and medical components. If you’re into welding tech or curious about how advanced joining methods work, ultrasonic welding is worth understanding.
How the Process Works
At its core, ultrasonic welding converts electrical energy into mechanical vibrations. These vibrations are delivered through a tool called a sonotrode, which presses against the materials being joined. As they vibrate against each other, localized friction generates heat—just enough to bond the surfaces without melting them.
The entire weld takes just a second or two. No arc, no fumes, and no mess.
Equipment and Setup
Ultrasonic welding machines look nothing like your usual TIG or MIG setup. They typically include:
- A power supply to create high-frequency energy
- A transducer that converts that energy into vibration
- A booster to increase vibration amplitude
- A sonotrode, which delivers pressure and vibration to the joint
This type of system is mostly used in production environments. Based on user feedback from manufacturing forums, these machines are easy to run once set up properly—but they’re not cheap or garage-friendly. Materials need to be clean, properly clamped, and perfectly aligned for consistent results.
Ease of Use and Learning Curve
If you’re used to traditional welding, ultrasonic welding feels like a whole different ballgame. There’s no visible heat, no bead to control, and no filler to manage. That said, many small-shop users report that once the machine is tuned, it produces consistent welds with minimal manual input.
You’re more likely to encounter this process in industries like:
- Electronics manufacturing
- Plastic packaging
- Medical device assembly
It’s not a DIY welding method, but if you work in automation or electronics, it’s a valuable tool.
Material and Safety Considerations
Ultrasonic welding works best with similar thermoplastics and thin, soft metals like copper or aluminum. It struggles with harder metals and isn’t well-suited for dissimilar metal welding—at least not without very specific equipment.
On the safety side, it’s considered lower risk than arc welding. There are no sparks, UV radiation, or toxic fumes. But the high-frequency vibrations and clamping force still require caution. Machines are often enclosed with built-in safeguards.
Conclusion
Ultrasonic welding is a clean, precise joining method that excels in fast-paced, automated environments. It’s not a fit for heavy fabrication or home shops, but in the right industry, it’s a game changer.
Pros:
- Fast and efficient
- Clean process with no sparks or fumes
- Great for plastic and thin metal parts
Cons:
- Limited to specific materials
- Expensive and not portable
- Requires precise setup and clean work surfaces
Whether you’re in high-tech manufacturing or just curious about welding innovations, understanding ultrasonic welding gives you insight into how the pros handle speed and precision.