Can You Weld Stainless Steel with a MIG Welder? Yes—Here’s How to Get It Right
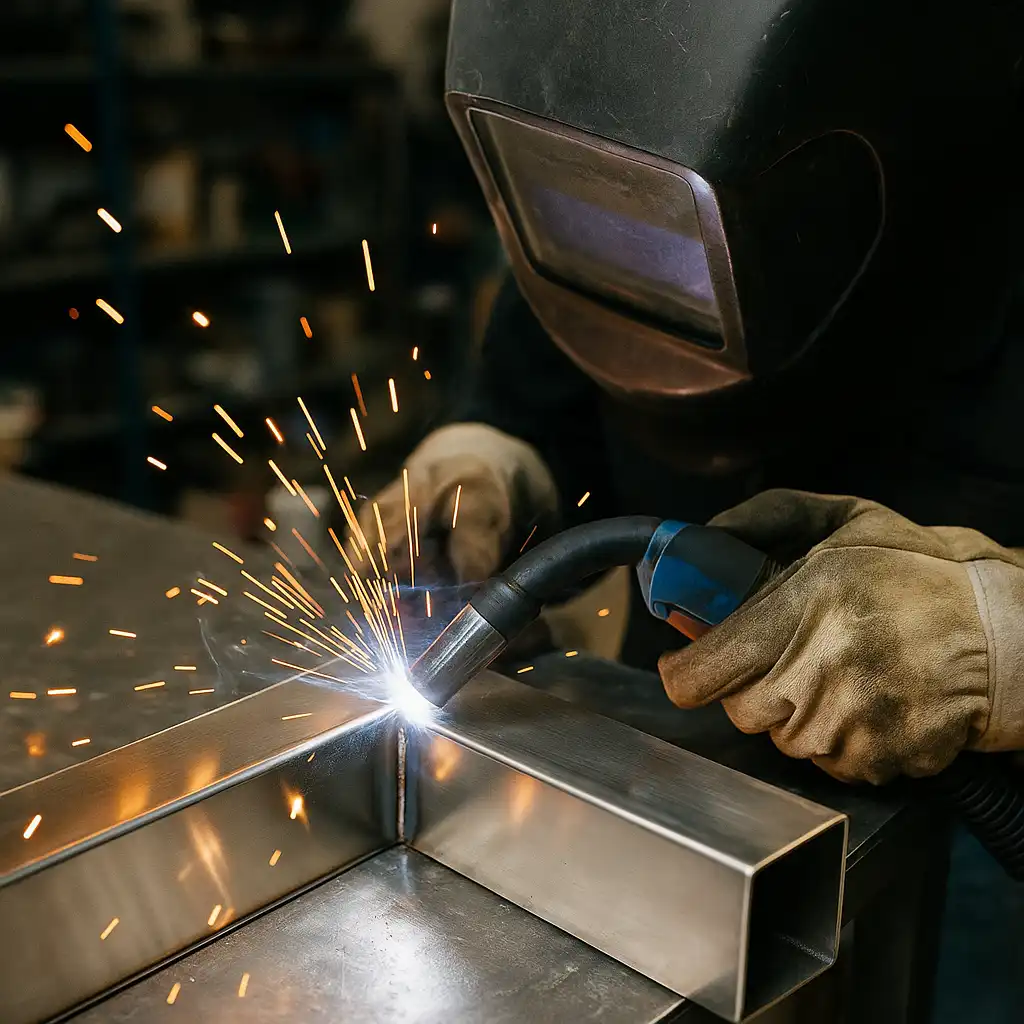
Disclosure: This post contains affiliate links. As an Amazon Associate, I earn from qualifying purchases—at no extra cost to you.
MIG welding stainless steel is not only possible—it’s practical for many real-world jobs. With the right wire, gas, and settings, even a basic MIG setup can produce strong, clean welds on stainless. That makes it a solid option for DIY projects, small shops, and quick repairs.
If you’re fabricating stainless brackets, patching a frame, or doing weekend work in the garage, MIG offers a beginner-friendly and efficient way to get it done.
What You’ll Need to Get Started
Most 120V and 240V MIG welders can handle stainless steel just fine. The key is using the correct wire and gas combination.
ER308L is the standard stainless wire for grades like 304 and 316. To protect the weld and improve appearance, most welders pair it with tri-mix gas (90% helium, 7.5% argon, 2.5% CO₂). Some also use 98/2 or 100% argon, but tri-mix delivers the cleanest results.
Based on user feedback, machines like the Lincoln 180 or Hobart Handler 210 work well for stainless projects up to about 1/8″ thick.
Tips on Learning Curve and Weld Quality
If you’re used to welding mild steel, stainless will feel familiar—but there are a few extra things to watch for. Stainless holds heat longer, which makes it more prone to warping and discoloration.
Short-circuit transfer mode works best for thinner material. Keep your travel speed steady and avoid dwelling in one spot. Tack often and give your work time to cool between passes.
Many hobbyists recommend doing a few practice runs on scrap before moving to your final piece. Once you dial in your voltage and wire speed, MIG can give you decent-looking results—especially for non-cosmetic welds.
Arc Performance and Cleanliness
Stainless MIG welds tend to produce more spatter and oxidation than mild steel. But with the right setup, you can still get a stable arc and clean beads.
Welders report that tri-mix gas reduces spatter and heat tint, making post-weld cleanup much easier. Some also suggest using a dedicated liner or gun for stainless to avoid contamination from carbon steel, which can lead to rust down the line.
Clean base material, proper shielding gas flow, and consistent torch angle all help improve bead appearance and reduce rework.
Is MIG Welding Stainless Worth It?
If you’re doing food-grade or aesthetic stainless welds, TIG is still the top choice. But for functional parts, general repairs, or small shop work, MIG is more than capable.
One thing to consider is cost. Tri-mix gas isn’t cheap, and not every welding shop keeps it in stock. If you’re on a tight budget or just need quick results, flux-cored stainless wire is another option. It doesn’t look as clean, but it gets the job done—especially for one-off repairs.
So if you’re working in a garage or handling occasional stainless jobs, MIG offers a practical, lower-cost entry point.
Conclusion
Yes, you can weld stainless steel with a MIG welder—and it’s a solid option for many light to medium-duty tasks. It’s easier to learn than TIG, more accessible than Stick, and great for quick setups and repairs.
Pros:
- Easy to learn
- Compatible with many home/shop MIG welders
- Good for repairs, brackets, and light fab work
Cons:
- Tri-mix gas is expensive and harder to find
- More spatter and tint than TIG
- Not ideal for polished or highly visible welds
If you’re welding stainless at home or in a small shop and need something simple and reliable, MIG is a smart, approachable way to go.
Related Articles You Might Find Helpful
Here are some guides to help with related stainless projects and beginner welding setups: