Is TIG Welding Better Than MIG for Clean, Precise Welds?
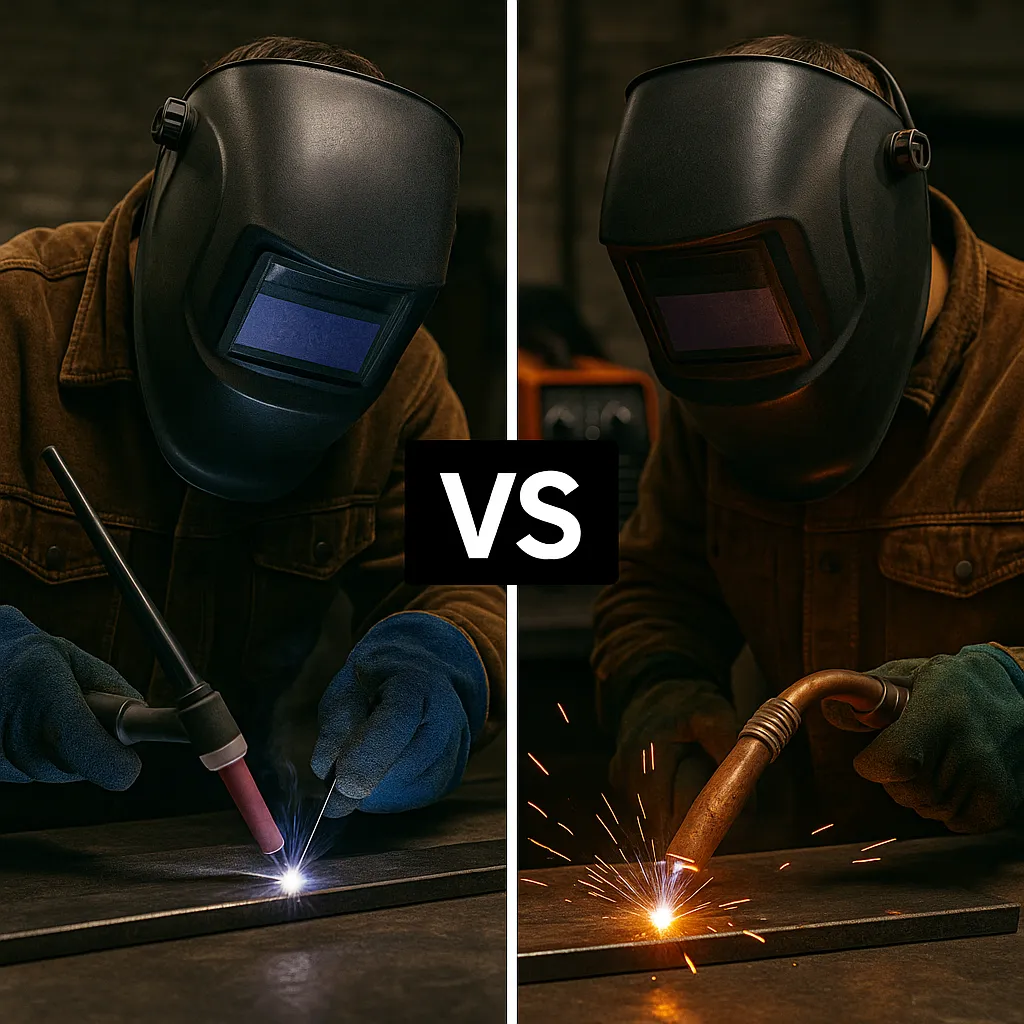
Disclosure: This post contains affiliate links. As an Amazon Associate, I earn from qualifying purchases—at no extra cost to you.
Choosing between TIG and MIG welding isn’t always straightforward—it depends on what you’re working on, how much control you want, and how fast you need to get the job done. Both methods are solid, but they serve different purposes depending on your goals, skill level, and shop setup.
Let’s dig into the key differences based on real-world use, welder feedback, and practical experience from the garage to the job site.
Arc Control and Weld Quality
TIG welding gives you precise control and a super clean finish. That’s why it’s the go-to for detailed work on thinner metals like stainless steel or aluminum. You can adjust the heat on the fly with a foot pedal, which helps lay down smooth, consistent beads—great for projects where appearance really matters.
MIG welding, though, is known for its speed and consistency. It handles thicker metals well and works efficiently for general fabrication, auto repair, and structural jobs. According to feedback from welding communities and user reviews, MIG is often preferred for its ease of use and reliability when working with mild steel.
So if you’re after top-notch precision, TIG takes the edge. But if time and productivity are key, MIG is tough to beat.
Ease of Setup and Learning Curve
MIG machines are plug-and-play for the most part. They’re simple to set up, and the learning curve isn’t steep. Even if you’re just getting started, it won’t take long to lay a decent bead. Plus, MIG is more forgiving when it comes to surface prep—perfect for shop work where conditions aren’t always ideal.
TIG, on the other hand, demands a cleaner work area and more coordination. You’ll need two hands to operate the torch and filler rod, and many setups use a foot pedal too. It takes time to get comfortable, and many beginners find it a bit frustrating early on. Still, if you’re aiming for fine detail, the payoff is worth it.
If you’re working in a small garage or just need to knock out a quick repair, MIG usually makes more sense. But if you’re looking to build skill and tackle precision work, TIG is worth learning.
Equipment Costs and Compatibility
TIG welders tend to cost more up front. You’ll also need extras like a foot pedal, high-frequency start, and 100% argon gas—none of which are cheap. And according to reviews, many welders eventually upgrade their torches or regulators for better performance.
MIG welders, especially dual-voltage or multi-process models, are typically more affordable and flexible. You can even run flux-core wire without shielding gas, which is great if you’re working outside or on a tighter budget.
So if cost and convenience matter, MIG is the practical choice. But if your focus is on high-quality finishes and you’re willing to invest, TIG delivers.
Value and Safety in Daily Use
Both methods require proper PPE, but TIG creates less smoke and spatter, which helps keep your work area cleaner. That said, TIG arcs can be intensely bright and hard on the eyes without the right helmet.
MIG is messier but faster, and many weekend welders say it’s more satisfying when you just want to get the job done. You’ll go through consumables quicker, but you’ll also move through your project faster.
From a value standpoint, MIG wins for versatility and ease. TIG wins when precision and presentation matter most.
Conclusion
TIG and MIG both have their strengths—it really depends on your project. TIG offers clean, precise welds and shines on thin metals, but takes more skill. MIG is faster, easier to learn, and great for thicker steel or general repairs. If you’re just starting out or working on everyday tasks, MIG is the practical pick. For fine detail and smoother beads, TIG’s worth the effort.